вайбер 099-63-72-507
ел. пошта marinalutay84@gmail.com
20.05.2020р. Технологічна послідовність виготовлення виробу. Властивості деревини.
Продовження роботи над проектом (продовження теми)
(2 академічні години)
Добрий день, дорогі учні! Опрацюйте, будь ласка, цей теоретичний матеріал. Ця інформація знадобиться вам у майбутньому.
Прийоми стругання ручним інструментом
Перед початком роботи ручним інструментом заготовку треба добре оглянути, визначити лицевий бік і напрям волокон. Стругати слід тільки у напрямі волокон – це полегшує працю і дає кращу поверхню. Заготовки кріплять на верстаті за допомогою гребінок або в лещатах так, щоб вони щільно прилягали до верстата.
Робітник має стояти впівоберта до верстата, корпус трохи нахилений уперед, ліва нога висунута вперед, паралельно верстатові, а праву ставить так, щоб кут між ступнями ніг становив 70 - 80°.
У процесі стругання треба правильно і надійно тримати інструмент і переміщувати його тільки рухами рук. Стругання будь-яким інструментом ведеться на повний розмах рук по прямій лінії. Чим менше рухів корпуса, тим менше втомлюється робітник. Натискати на інструмент треба рівномірно, щоб не завалити деталь на кінцях, тому на початку стругання заготовки більше натискають на передню частину колодки, а в кінці – назадню. Під час руху інструмента назад задню частину колодки трохи піднімають, щоб запобігти зашліфовуванню леза різця.
Якщо із заготовки потрібно зняти товстий шар деревини, то стругання починають шерхебелем. Після цього поверхню вирівнюють одинарним рубанком. Остаточно вирівнюють подвійним рубанком або фуганком, рухаючи їх поверхнею у напрямку волокон, а в завилькуватих і сучкуватих місцях тримаючи під гострим кутом.
Рівність площини перевіряють лінійкою, кутником або двома однаковими за товщиною брусками. Якщо площина вистругана правильно – грані брусків зіллються в одну лінію, якщо ні – то вони перетинатимуться.
Тема 4.5. Процес розмічання та виготовлення шипового з’єднання
Види з’єднань. Шипові з’єднання. Розмічання шипового з’єднання. Послідовність виготовлення одинарного шипового з’єднання.
Запилювання. Довбання деревини. Долота і стамески, їх призначення.
Глухі та наскрізні отвори. Прийоми роботи столярним інструментом під час виготовлення шипових з’єднань.
Припасування елементів шипового з’єднання. Затискні пристрої: струбцини, гвинтовий прес, їх використання в столярній справі.
Види з’єднань деталей з деревини
Дерев’яні деталі з’єднують між собою цвяхами, шурупами, болтами, а також за допомогою різноманітних столярних з’єднань.
Більшість меблевих виробів мають прямокутну форму, тобто деталі, складальні одиниці і групи з'єднуються під прямим кутом. Найбільш поширене з'єднання брусків – шипове. Воно складається з двох елементів – шипа і провушини або гнізда (мал. 4.13). Залежно від необхідної міцності з'єднань і товщини деталей може бути виготовлено один, два, три і більше шипів. Збільшення кількості шипів збільшує площу склеювання, а значить, і міцність з'єднання виробу в цілому.
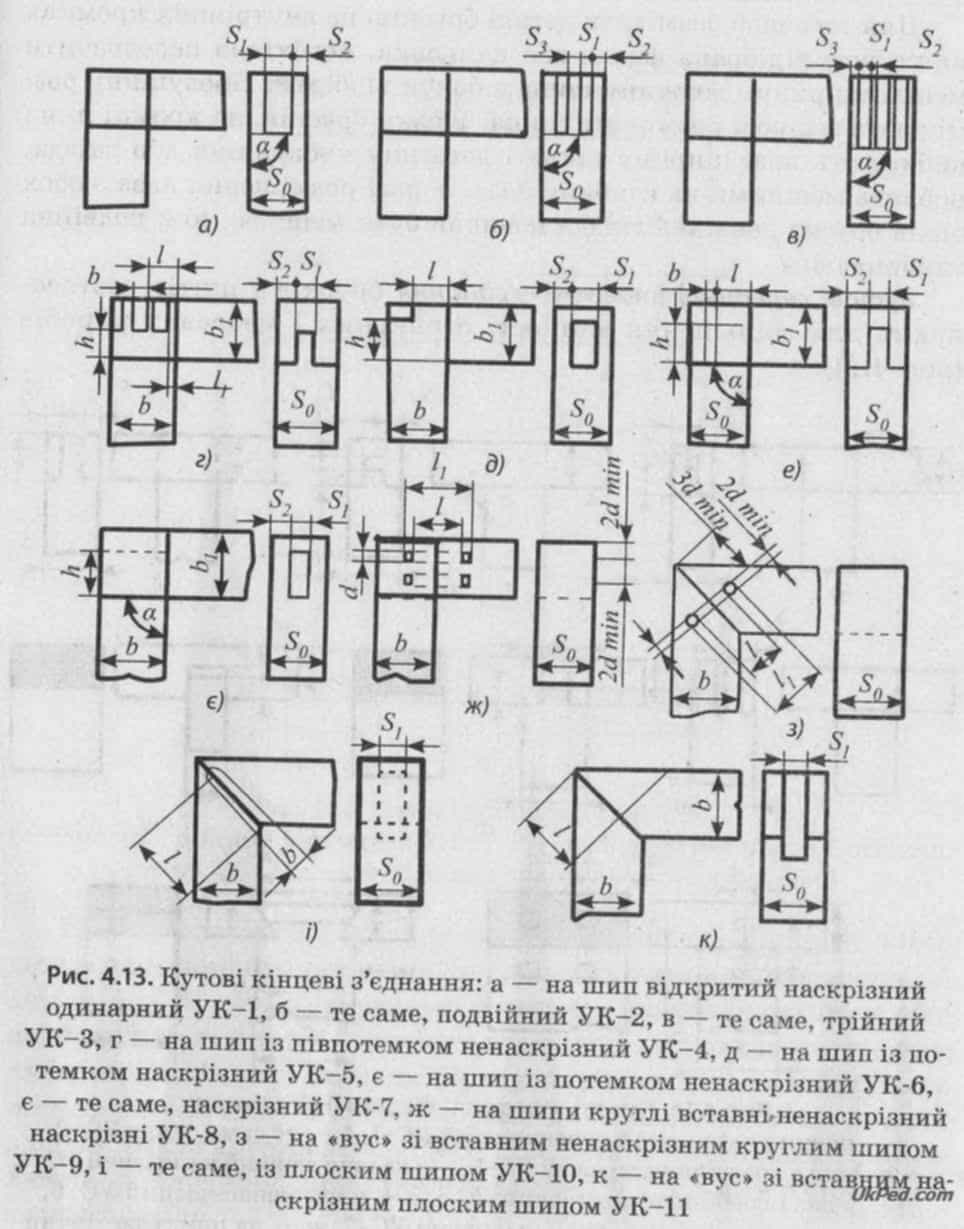
Розміри і форма деталей і їх з'єднувальних елементів визначаються кресленням. Для перенесення цих розмірів на деталь і точного її виготовлення необхідно зробити розмітку підготовленим інструментом. Розмічають деталі за допомогою кутника, загостреного олівця і рейсмуса, проводячи всі риски з лицьового боку. Однакові деталі краще розмічати разом, для чого розміщують їх поряд і скріплюють.
Для того щоб, розмітити деталі брусків, на внутрішніх кромках яких буде відібрана фаска або кальовка, необхідно передбачити менші ширину і довжину шипа зі сторони відбірки. Провушину розмічають згідно з розмірами шипа. В'язки брусків, на кромці яких вибирають паз, ширину шипа і довжину провушини або гнізда, роблять меншими на глибину паза. При розміщенні паза з обох сторін бруска довжина гнізда повинна бути меншою, ніж подвійна глибина паза.
Кутові серединні (таврові) з'єднання брусків і щитів застосовують для збільшення міцності столярних і меблевих виробів(рис. 4.14).
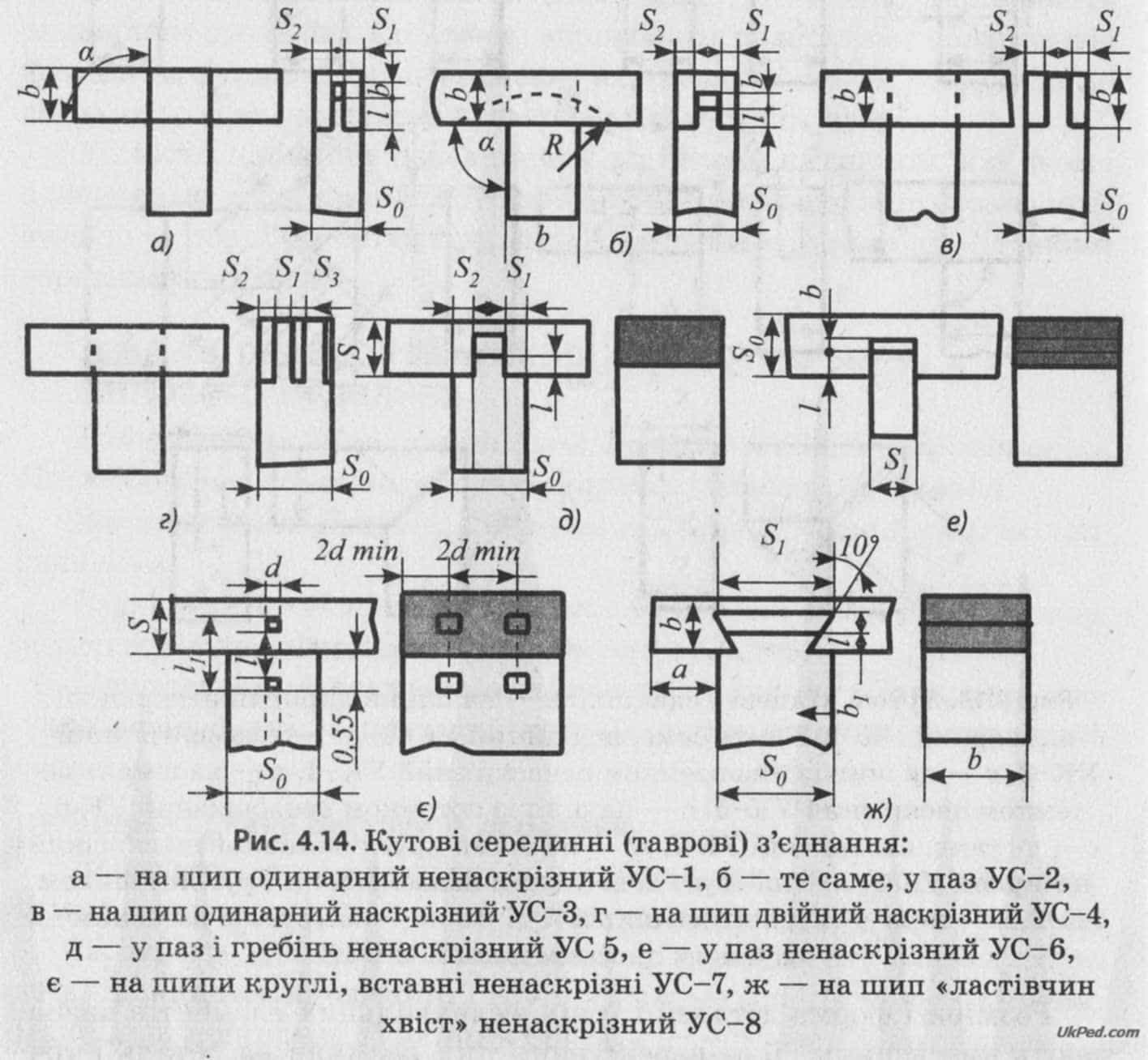
Кутові ящикові з'єднання. Для цих з'єднань застосовують різноманітні ящикові шипи (рис. 4.15). При виготовленні кутових ящикових з'єднань на одному торці деталі роблять шипи, а на другому – провушини, тому точність виготовлення стінок ящиків або коробок повинна бути високою.
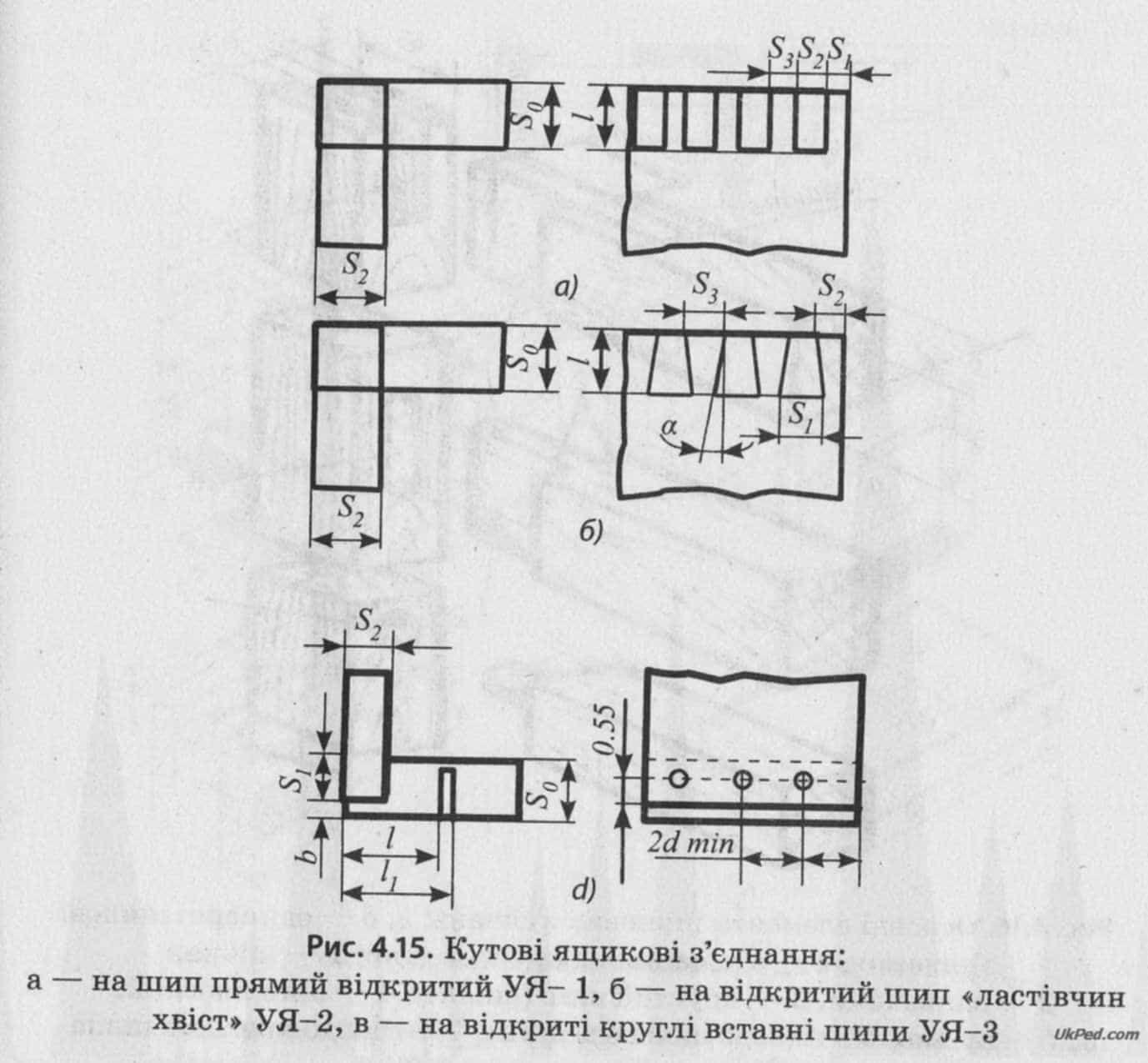
При кутовому з'єднанні на прямі ящикові шипи на кінці деталі за допомогою рейсмуса відкладають товщину деталі, що приєднується. Розмічають з'єднувальні елементи, наносячи риски на обидві сторони деталі й торці. Розмітку провушин слід виконувати з урахуванням щільності з'єднань. Провушини видовбують долотом або стамескою спочатку з однієї сторони до половини деталі, а потім з іншої. Після виготовлення провушин деталь цим торцем встановлюють на площину спряжувальної деталі під прямим кутом і розмічають шипи.
Якщо треба, щоб з однієї сторони з'єднання не було видно шипів, його роблять напівпотайним. Для цього деталь, на одній стороні якої не буде видно торців шипів (передня стінка ящика), виготовляють товщою, ніж деталь, що приєднується (бокова стінка ящика). Ящикові з'єднання найраціональніше розмічати за допомогою шаблонів.
Основні елементи шипових з'єднань подані на мал. 4.16.
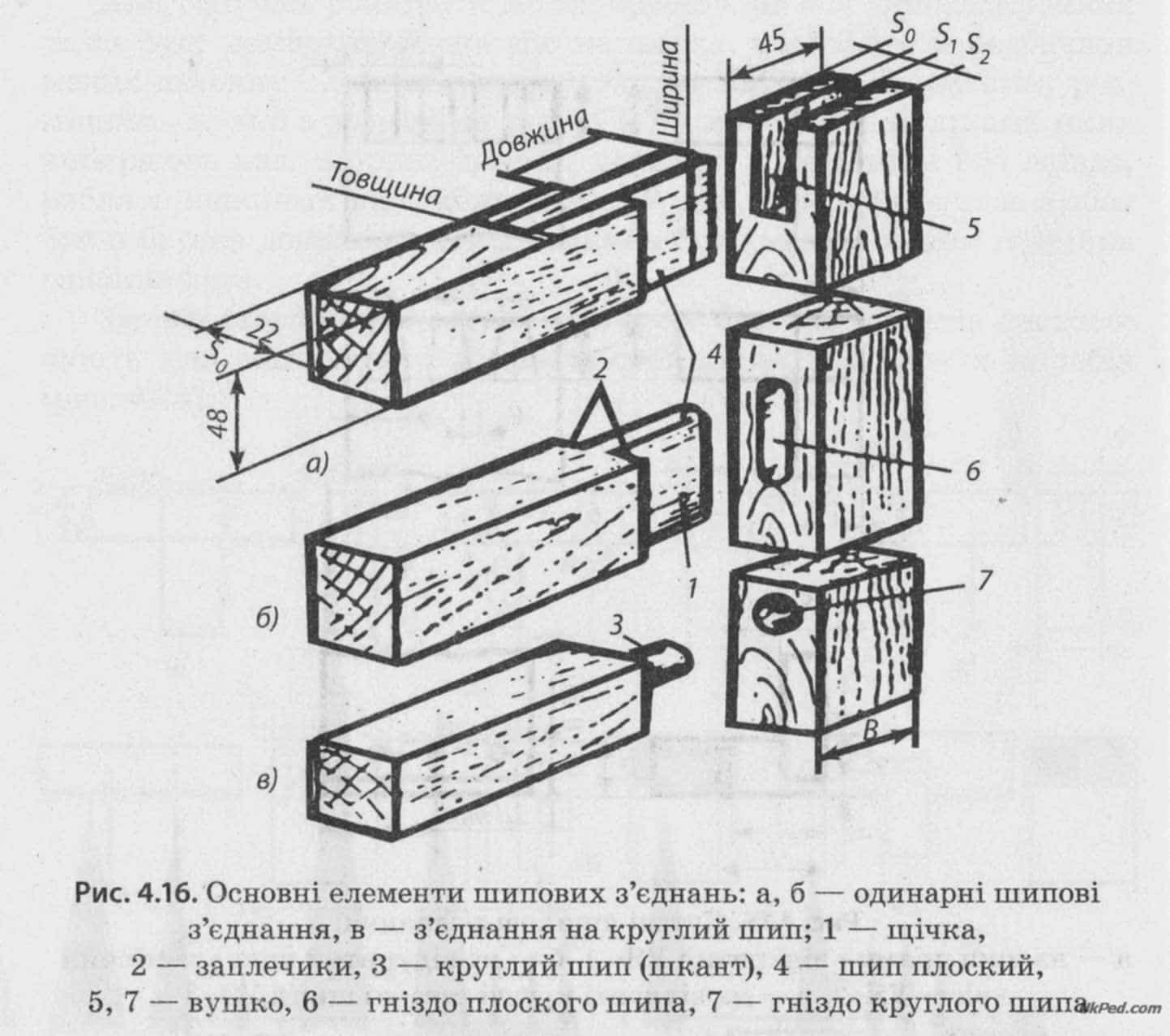
Для розмічання одинарного шипа і вушка беруть необторцьовані бруски, кладуть у ряд на верстак, щільно притискають один до одного лицьовим (базовим) боком уверх і вирівнюють їх кінці. Потім за допомогою кутника проводять контрольну лінію (мал. 4.17, а), від якої відкладають ширину брусків і проводять за допомогою кутника другу лінію. Перша риска буде означати місце торцювання, друга – місце заплечиків. Потім за допомогою кутника проводять лінії навколо бруска, причому при замиканні бруска кінці ліній повинні збігатися.
При з'єднанні фальцьованих брусків від лінії, проведеної на відстані ширини бруска від торців, проводять на всіх брусках ще одну лінію на відстані, яка дорівнює ширині фальца. При виготовленні шипів один заплечик зарізають до цієї лінії (мал. 4.17, б). Для випилювання вушка пропил іде у видовбаній частині деревини. При цьому половина риски зрізається, а друга половина залишається на стінках вушок.
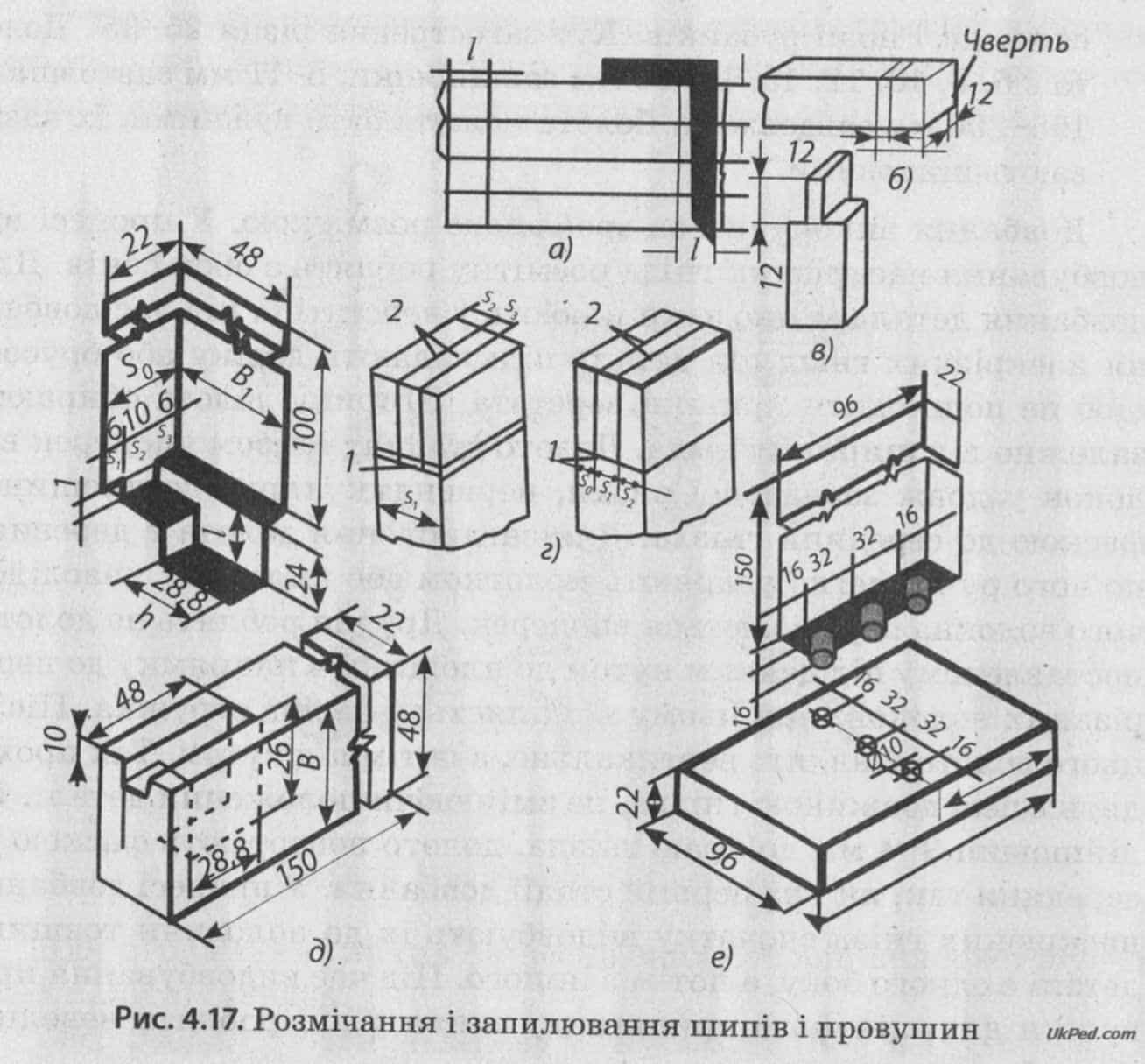
Для запилювання пилку з дрібними зубцями ставлять на ближче ребро під кутом 15-20° до торця і спочатку роблять три-чотири рухи на себе, не сильно тиснучи на неї. Коли полотно пилки заглибиться, пилку переміщають рівномірно в обидва боки.
Необхідно слідкувати, щоб не заглиблювати пропили за риски. Для довбання вушок наверстаку закріплюють брусок струбцинами і довбають спочатку до половини товщини бруска, а потім повертають брусок і продовжують довбати.
Довбання деревини.Для надання деталям остаточної форми, тобто для виготовлення з'єднувальних елементів (прямокутних наскрізних і ненаскрізних отворів і вушок), застосовують долота і стамески.
Долото – це металевий стиржень прямокутної форми, у нижній (робочій) частині якого є різець, а у верхній – заплечики і конусоподібний хвостовик, на який насаджують дерев'яну ручку, виготовлену з деревини твердолистяних порід (граб, бук та ін.). Лезо різця має пряму різальну кромку, яка утворюється внаслідок перетину передньої і задньої граней і гостриться так само, як і ножі рубанків. Кут загострення різця 25–35◦. Долота бувають 6, 8, 10, 12, 15, 18, 20 мм завширшки, 8-11 мм завтовшки, 165 - 200 мм завдовжки. Долота можуть бути вужчими, їх називають шиповими.
Довбання виконують за зробленою розміткою. У процесі видовбування наскрізних гнізд розмітку роблять з обох боків. Для довбання деталь міцно закріплюють у верстаті, а при довбанні наскрізних гнізд під деталь підкладають дошку або брусок, щоб не пошкодити кришки верстата. Ширину долота обирають залежно від ширини гнізда. Долото ставлять лезом упоперек волокон уздовж зазначеної риски, перпендикулярно до площини, фаскою до середини гнізда. Для заглиблення долота в деревину по його ручці легко ударяють молотком або киянкою, унаслідок чого волокна перерізаються впоперек. Другий роблять по долоту, поставленому під деяким кутом до площини в напрямку до перерізаних волокон, при цьому відділяється перша стружка. Після цього долото ставлять вертикально, а потім під кутом. Так проходять всією довжиною гнізда, не змінюючи положення деталі. Не дійшовши 3-4 мм до краю гнізда, долото повертають фаскою до середини так, як і при першій стадії довбання. У процесі довбання наскрізних гнізд спочатку видовбують їх до половини товщини деталі з одного боку, а потім з другого. При видовбуванні провушин для щільного прилягання шипа у дні роблять невеликі заглиблення.
Стамески – дуже подібні до доліт, тільки значно тонші (3-5 мм). Вони можуть бути плоскими або напівкруглими. Ширина плоских стамесок: 4, 6, 8, 10, 12, 15, 20, 25, 30, 40, 50 мм; напівкруглих - 6, 8, 10, 12, 15, 20, 25, 30, 40 мм. Фаска в напівкруглої стамески – з опуклого боку. Кут загострення стамесок 15–20 %. Стамески і долота гострять так само, як і ножі рубанків.
Плоскі стамески застосовують для довбання неглибоких гнізд у тонких деталях, зачищення їх, обрізання торців, стругання кромок, зачищення і зняття фасок на кромках деталей і щитів. Напівкруглі стамески застосовують для видовбування криволінійних отворів та обробки криволінійних поверхонь. Довбання стамесками здійснюють так само, як і долотами, а різання натискуванням правою рукою на торець ручки, причому ліва притискує лезо до матеріалу і спрямовує по наміченій лінії.
У багатьох випадках для надання деталі відповідної форми струганням зручно користуватись стамесками.
Стамеску при струганні тримають тільки двома руками: правою за ручку, а лівою за залізко. Деталь повинна бути міцно закріплена в лещатах верстака як показано на мал. 4.18.
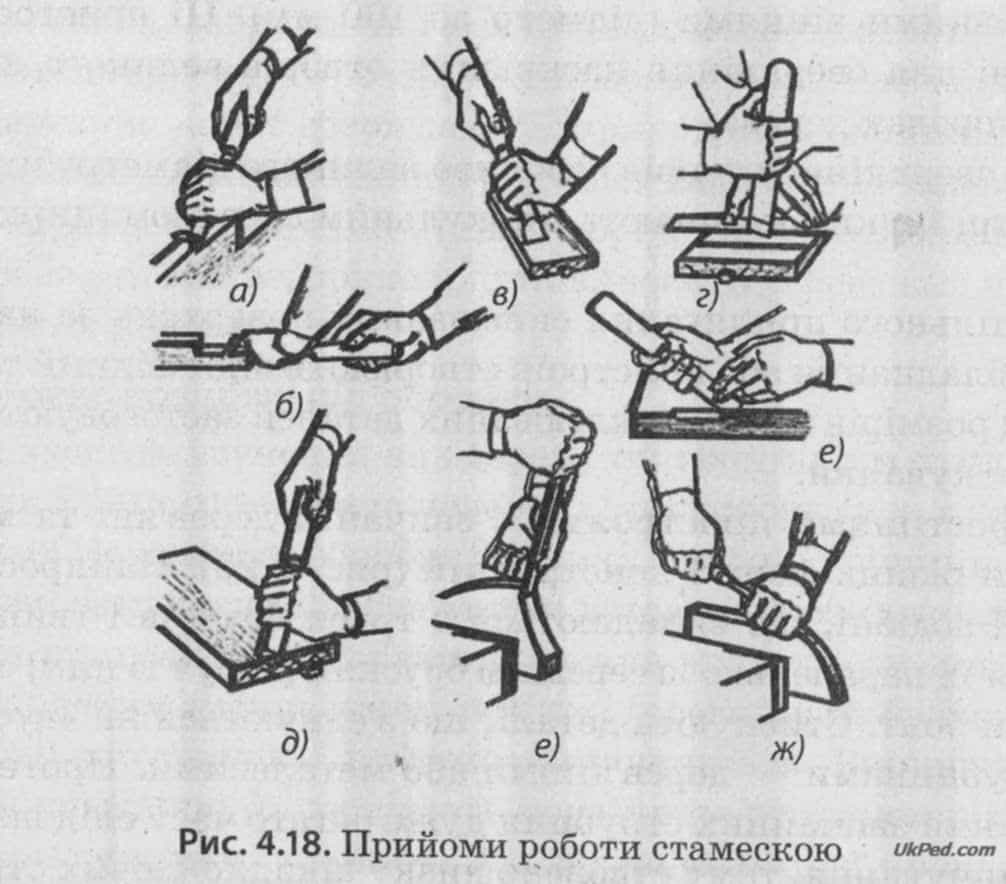
Для отримання глухих та наскрізних отворів використовують різноманітні свердла.
Свердла для роботи по дереву бувають (рис. 2.19):
1) перовими або плоскофрезерними (діаметр до 40 мм). Ними дуже зручно працювати, завдяки серединній відцентровці (вони не йдуть убік);
2) гвинтовими (діаметр до 32 мм). Цей вид свердел зазвичай використовується для свердління отворів великої глибини (стандартні розміри 200/300/450 мм);
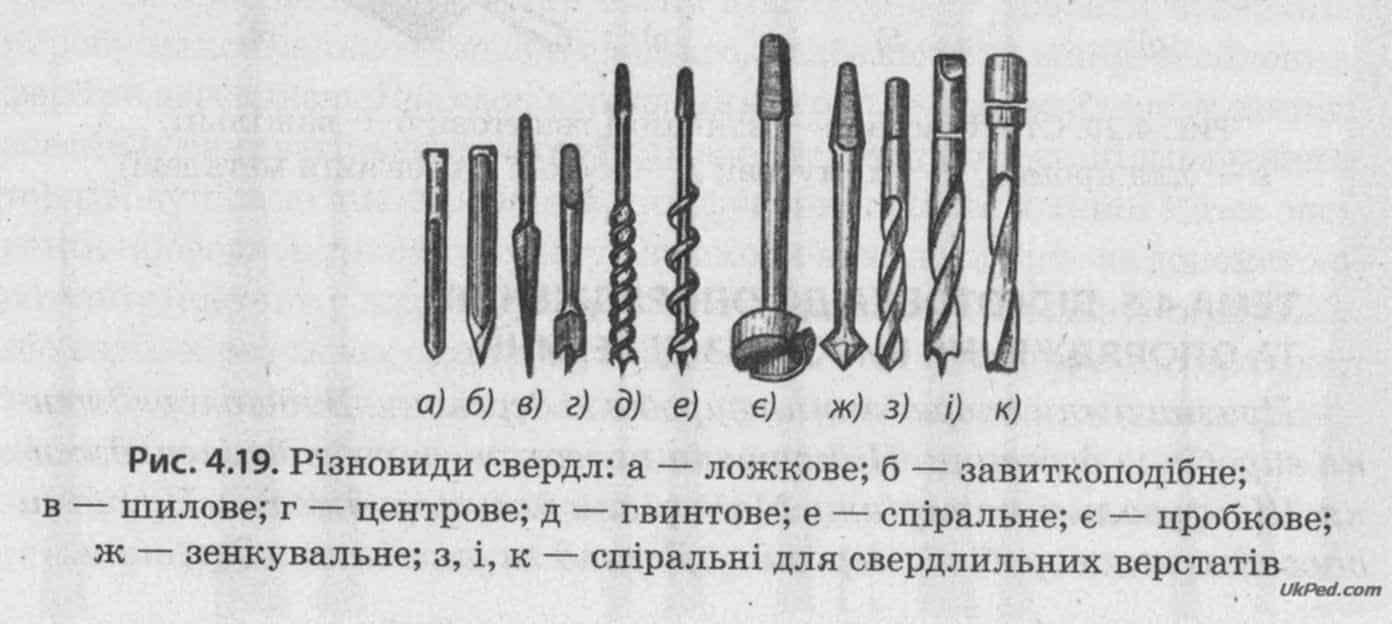
3) корковими. Основним призначенням і особливістю цього типу свердел є можливість свердління глухого отвору достатньо великого діаметру (наприклад, для кріплення петель у дверцях шафи);
4) пильними вінцями (діаметр до 100 мм). Ці пристосування призначені для свердління наскрізних отворів великого діаметру в різних породах дерева;
5) для свердління отворів особливо великого діаметру призначений пристрій, який називають циркульним свердлом (циркульним різцем).
Для щільного прилягання склеюваних поверхонь за наявності певного обладнання або пристроїв створюють відповідний тиск. Залежно від розмірів і форми склеюваних деталей застосовують також різне устаткування.
Найпростішими пристроями є звичайні дерев'яні та металеві струбцини різних форм і конструкцій (мал. 4.20). Найпростішими з них є П - подібні, що складаються з трьох брусків і гвинта. Для зміцнення їх паралельно із середнім бруском (поруч із ним) ставлять металевий болт. Стискують деталі, що з'єднуються на «вус», кутовими струбцинами – дерев'яними або металевими. Проте при застосуванні звичайних струбцин дуже багато часу слід витрачати на розгвинчування, тому створено ряд швидкодіючих струбцин.
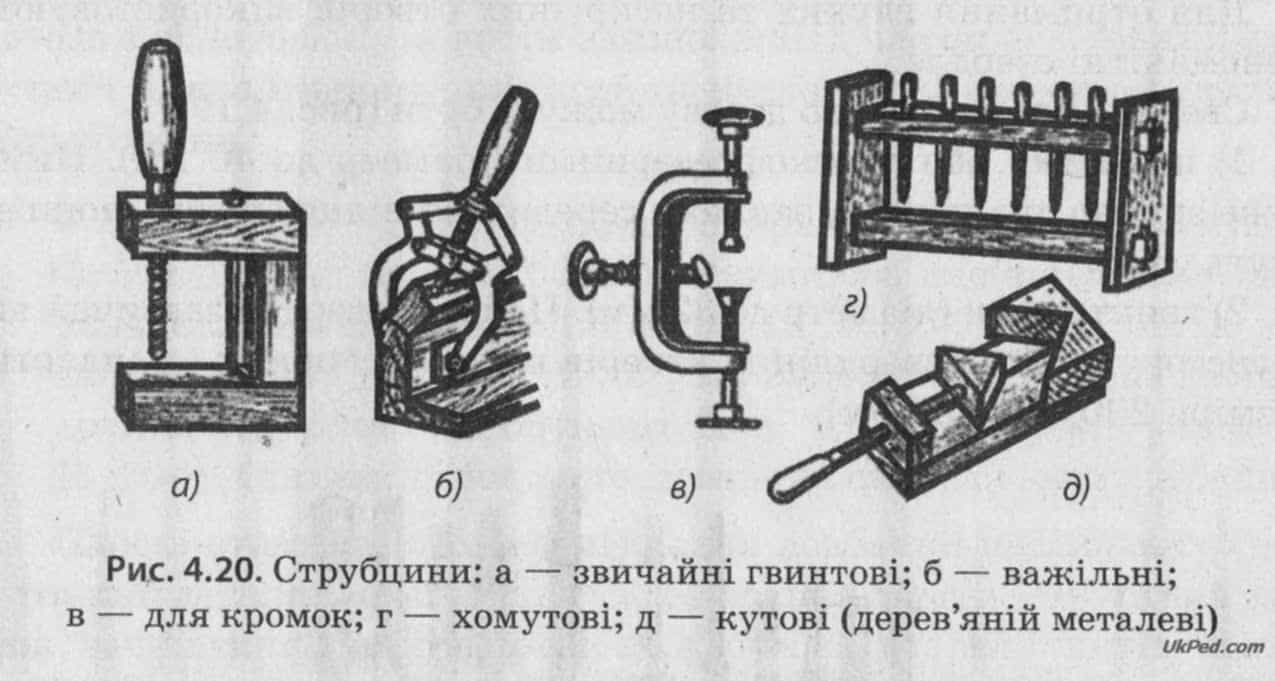
Тема 4.6. Підготовка до опорядження та опорядження виробу із деревини
Призначення опорядження виробів із деревини. Види опорядження виробів із деревини. Підготовка поверхонь виробу до опорядження. Шліфувальні матеріали. Матеріали для опорядження. Прийоми опорядження виробів із деревини. Догляд за виробами з деревини.
Під опорядженням деревини розуміють створення на її поверхні захисного декоративного покриття з метою поліпшення зовнішнього вигляду і захисту від дії навколишнього середовища (повітря, вологи, світла, тепла, забруднень і механічних пошкоджень).
Захисні покриття бувають прозорі й непрозорі. Перші не тільки захищають деревину, але і зберігають її природний зовнішній вигляд, підкреслюючи малюнок (текстуру). Застосовуються вони зазвичай для обробки виробів із деревини цінних порід, які мають красивий малюнок поверхні. Непрозорі покриття наносять головним чином на вироби з малоцінних порід дерева.
Підготовка поверхні під обробку
У цю операцію входить усунення вад деревини: тріщин, ум'ятин, сучків, що випали й інших дефектів поверхні, які утворилися в результаті попередньої механічної обробки. Великі, глибокі тріщини, щілини і порожнечі закладають дерев'яними вставками на клею, дрібні заповнюють шпаклівкою. Вм'ятини можна усунути як шпатлюванням, так і рясним змочуванням зам'ятої деревини: ввібравши вологу в себе, вона набубнявіє, і вм'ятина вирівняється. Вирівнявши підготовлену поверхню, її стругають подвійним рубанком, з тим, щоб зробити максимально гладкою. По завершенні цієї процедури поверхню протирають вологим тампоном і після висихання шліфують дрібнозернистою шліфувальною шкіркою або пемзою, щоб усунути дрібні ворсинки, що роблять поверхню шорсткою. Цю операцію повторюють кілька разів. Якщо оброблювана деревина твердої породи, то ворсинки прибирають циклюванням (для м'яких порід цикля не годиться, тому що вона не зрізає, а лише приминає ворс на них).
Далі здійснюють повторну зачистку. Сюди входить повторна зачистка ріжучими інструментами (у разі необхідності), підмазування пастами, шліфування шкіркою і пемзою, знесмолювання деревини і грунтування поверхні. Мета цього етапу підготовки – зробити поверхню виробу максимально рівною і гладкою і забезпечити міцне зчеплення фарби з деревиною. Порядок проведення опоряджувальних робіт такий: знесмолювання (тільки для хвойних порід), ґрунтування, підмазування торців, суцільне шпаклювання, шліфування. Після кожної з цих операцій проводиться тривала сушка. Знесмолювання роблять за допомогою розчину ацетону у воді (1:3) або сумішшю ацетону і пральної соди (1:4), або водним розчином соди, нагрітим до 60-70°С. Ганчіркою або щіткою, змоченою в одному з цих розчинів, протирають поверхню деревини, після чого залишки розчину змивають теплою водою.
Слід мати на увазі, що перше шліфування виконується як уздовж, так і впоперек волокон, а останнє, остаточне, – тільки уздовж. Ідеально рівної поверхні можна досягти за допомогою шпаклівки, яку наносять на поверхню виробу, заповнюючи всі тріщини, западини і вм'ятини. Дерев'яні вироби шпатлюють клейовими, олійними, напівмасляною і лаковими шпаклівками. Клейову шпаклівку можна приготувати з рідкого столярного клею, крейди і оліфи. Готовий розчин наносять рівним шаром на поверхню. Тонкий шар його сохне 2-3 години. Після цього поверхню знову шліфують. Зазвичай ця операція виконується шліфувальною шкіркою – спочатку крупнозернистою, а в кінці – дрібнозернистою. Шліфують, як правило, вздовж волокон, але тверду деревину можна шліфувати і упоперек волокон. Після правильно проведеного шліфування виріб можна фарбувати.
Для шліфування поверхні деревини, шпакльованих, ґрунтованих, лакових і інших покриттів застосовують різні шліфувальні матеріали: шкірки, порошки й пасти.
Шліфувальна шкірка – це абразивний гнучкий матеріал,що є гнучкою основою, на поверхню якої нанесений абразивний порошок різноїзернистості. Призначена для сухого або мокрого шліфування. Шкірки вітчизняного виробника виготовляють двох типів – рулонні (Р) і листові (Л). Розміри аркушів і довжина рулонів різні. Шліфувальні матеріали – абразиви бувають – скляні, кремнієві, кварцитові різної зернистості. Номери зернистості: 40, 32, 25, 20, 16, 12, 10, 8, 6, 5, 4: М63, М50, М40, М28, М20, М14. Шкірка з літерою М перед номером називається мікронною, тобто дуже дрібною. Перший раз шліфують шкурками № 16-12 з поступовим зменшенням зернистості.
Шліфувальні порошки – сухі абразивні зерна. Лакофарбові покриття шліфують порошком пемзи або трепелу, найчастіше зі змочувальними рідинами: скипидаром, гасом, олією, водою.
Шліфувальні пасти – абразивний порошок (пемзи, трепелу, електрокорунда, карбіду кремнію), розтерті на легкорозчинній суміші, що не висихають, різноманітні олії, віск, парафін тощо. Розчинниками служать скипидар, гас, уайтпспірит, а розріджувачем – вода.
Полірувальні суміші (політури) застосовують для надання лакофарбовим покриттям більшого блиску, а також для їхнього вирівнювання.
Непрозора обробка. Для непрозорої обробки використовують клейові, масляні або емалеві фарби. Міцні й водостійкі покриття отримують при фарбуванні дерев'яних виробів масляними (алкідними) фарбами і емалями. Вони захищають деревину не тільки від загнивання, але і від деформації, а тому особливо підходять для фарбування меблів і предметів на кухні та у ванній кімнаті, а також у передпокої і коридорі. Забарвлення алкідними фарбами здійснюють м'якими пензлями зі щетини. Емаль перед використанням рекомендується підігріти на водяній бані до 50-70° С. Нітроемалі наносять за допомогою фарборозпилювача в 4-5 шарів. При цьому кожен попередній шар обов'язково шліфується дрібною шліфувальною шкіркою. Останній шар зазвичай полірують із використанням спеціальної пасти. Майте на увазі, що нітроемалі не можна наносити на покриття з масляної фарби, оскільки нітроемаль розчиняє цю фарбу.
Прозора обробка. Як уже зазначалося, це спосіб обробки столярних виробів із деревини цінних порід. Прозоре покриття може бути глянсовим, матовим, оксамитовим або дзеркальним. Процес підготовки поверхні під прозоре покриття такий же, як і під непрозоре. Але всі операції необхідно проводити більш ретельно.
Домашнє завдання. Опрацюйте, будь ласка, цей теоретичний матеріал та зробіть дуже стислий конспект (можна у вигляді тез).
Фото відповідей надсилайте у вайбер 099-63-72-507
або на ел. пошту marinalutay84@gmail.com
Продовження роботи над проектом (2 академічні години)
Добрий день, дорогі учні! Опрацюйте, будь ласка, цей теоретичний матеріал. Ця інформація знадобиться вам у майбутньому.
Вибір деревини для виготовлення виробу.
Різноманітні деревообробні ремесла здавна були поширеними на території всієї України, бо деревина – це універсальний матеріал, із якого можна було виготовити багато необхідних речей: посуд, меблі, іграшки, прикраси, знаряддя праці, човни, мости, вози, сани, будівлі. Сьогодні з неї виготовляють тисячі різних виробів найменувань. Це насамперед меблі різноманітних видів і призначення, деталі будівель і споруд, численний господарський та спортивний інвентар, музичні інструменти.
Для того, щоб правильно підібрати деревину для виготовлення конкретного виробу, визначити доцільні способи обробки, потрібно враховувати особливості її структури: неоднорідність та розташування волокон, які проходять уздовж стовбура.
Із стовбура дерева шляхом розпилювання його на частини одержують пиломатеріали (мал. 4.1).
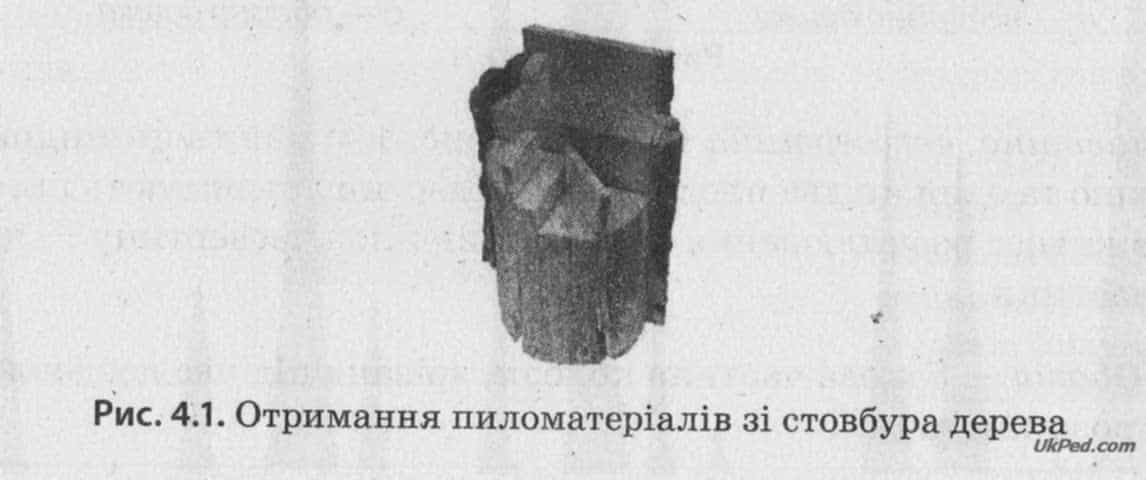
Пиломатеріали отримують у результаті поздовжнього розпилювання колод на спеціальних верстатах – пилорамах.
Колоди – це круглі лісоматеріали, які використовують цілими або як сировину для пиломатеріалів.
За формою і розмірами поперечного перерізу пиломатеріали поділяють на бруси, бруски, дошки, обаполи і шпали (пиляні деталі).
Бруси – це пиломатеріал квадратного чи прямокутного перерізу. Залежно від кількості пропиляних сторін вони бувають двокантні, трикантні й чотирикантні (мал. 4.2). Пиломатеріал такого ж перерізу, але товщиною до 100 мм і шириною не більше подвійної товщини називають брусками.
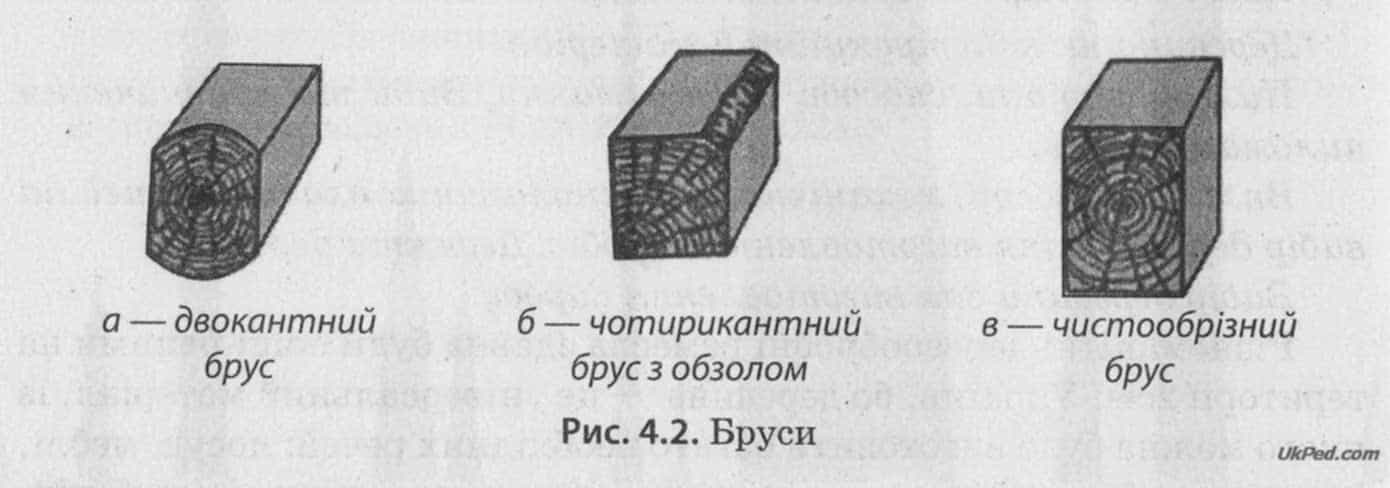
Дошки – це пиломатеріал прямокутного перерізу товщиною до 100 мм шириною, більшою за подвійну товщину. Дошки бувають обрізні, необрізні, обрізні з обзолом (мал. 4.3).
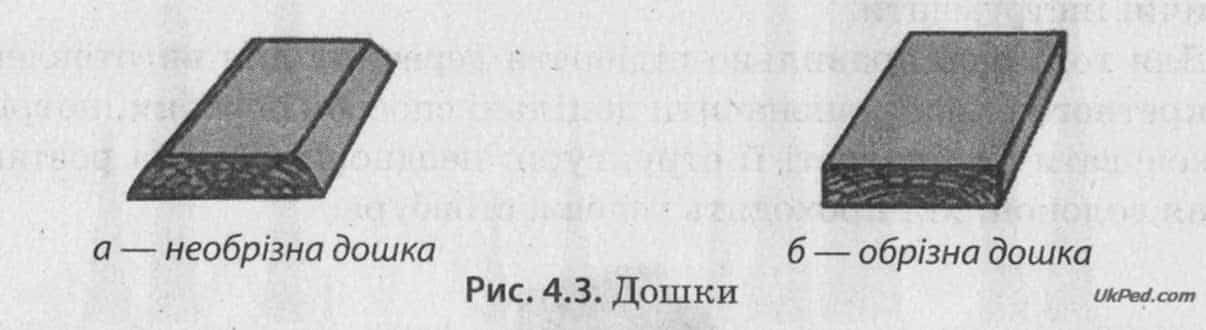
Пластина, четвертина та обапіл (мал. 4.4) мають циліндричну поверхню та один чи два плоскі зрізи. Пластина отримується шляхом поздовжнього розпилювання чурбака навпіл, а четвертина – на чотири частини.
Обапіл – бокова частина колоди, зрізана при поздовжньому розпилюванні.
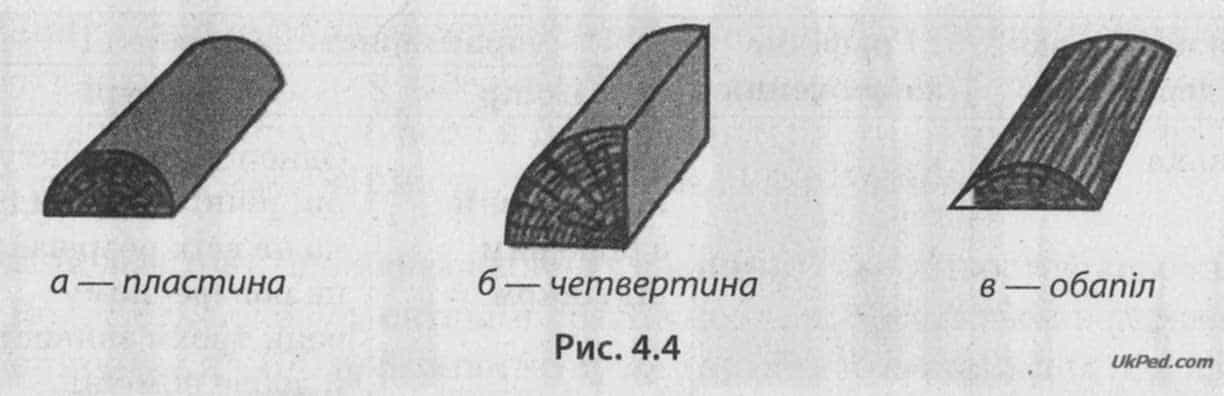
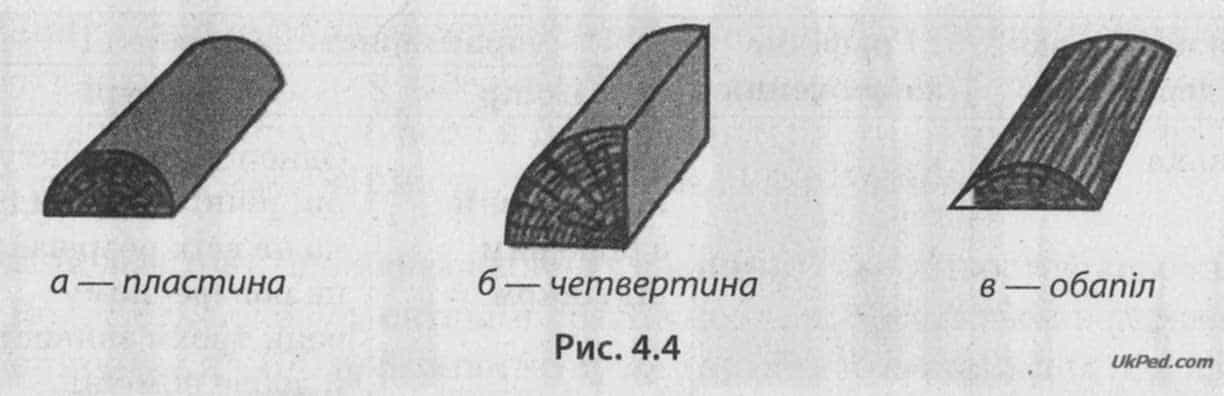
Загальні властивості деревини як конструкційного матеріалу.
Широке використання деревини як конструкційного матеріалу зумовлене її унікальними властивостями. Деревина є досить легкою, порівняно м'якою, і тому є досить легкою в обробці. Важливою технологічною властивістю деревини є здатність утримувати металеві кріплення, наприклад, цвяхи, шурупи. Незважаючи на описані загальні характеристики деревини, її властивості відрізняються залежно від породи.
При виборі деревини для виготовлення виробів необхідно враховувати її властивості, зокрема фізико-механічні, технологічні та фізичні.
Зовнішній вигляд поверхні деревини (текстура, блиск, колір) та її запах – фізичні властивості деревини, які можна визначити органолептичним способом. Аналіз комплексу цих характеристик дозволяє встановити породу деревини (табл. 4.1).
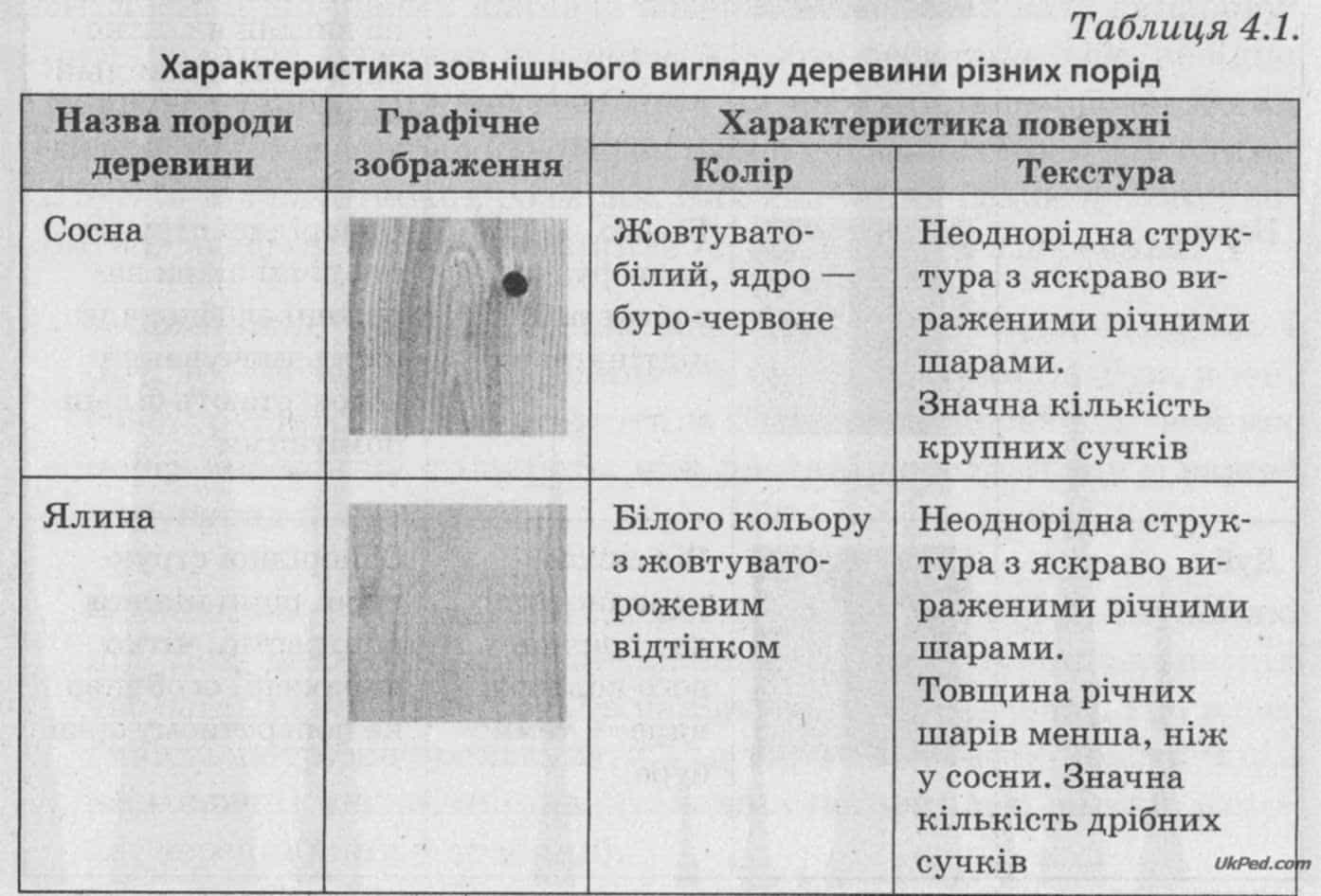
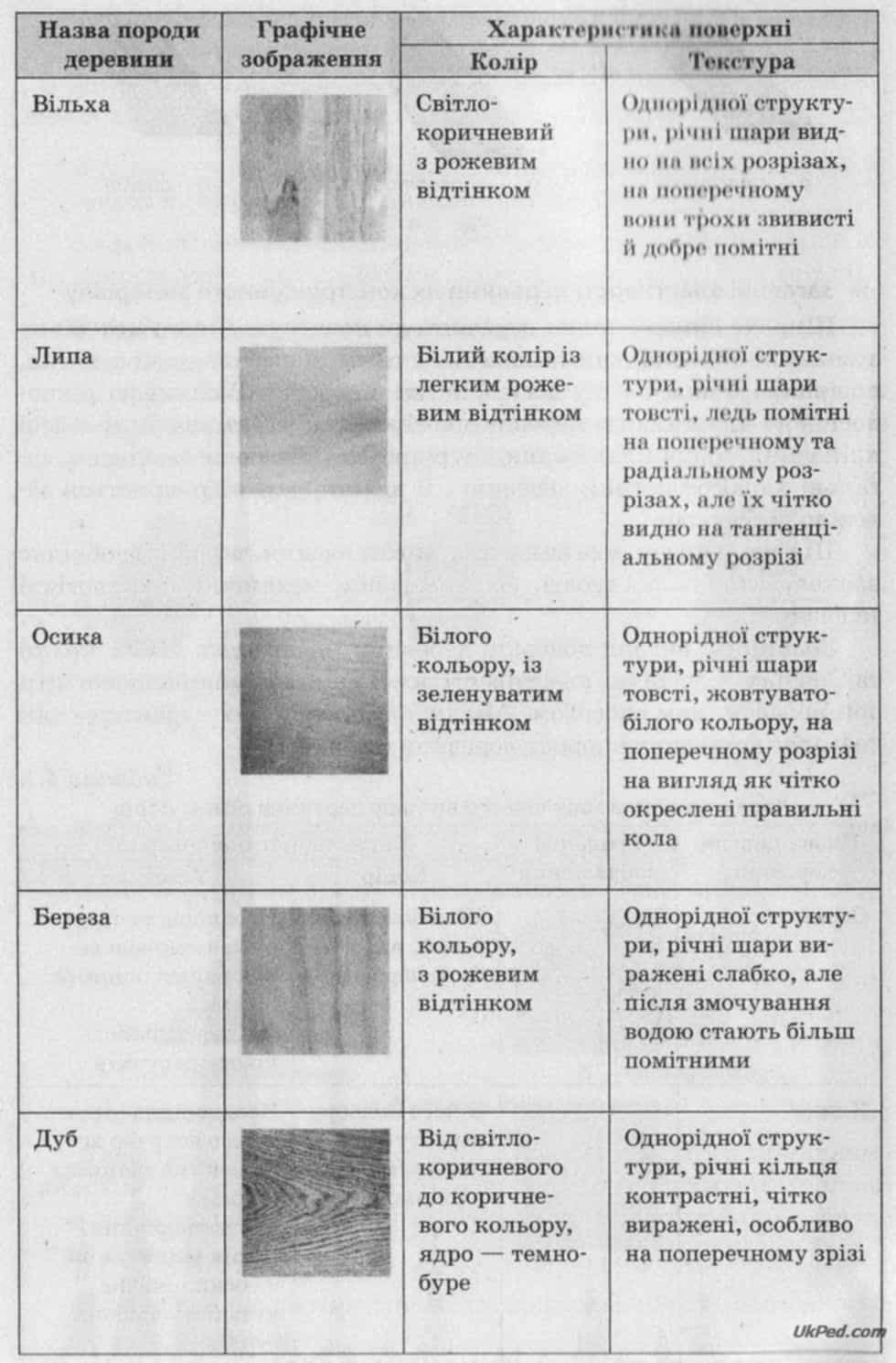
Зовнішній вигляд поверхні деревини дуже впливає на естетичні якості виробу. Але для забезпечення усіх споживчих та виробничих вимог потрібно враховувати й інші характеристики цього матеріалу, зокрема вологість, міцність, щільність, твердість тощо.
Вологість є однією з основних фізичних властивостей деревини. Вологість показує, скільки грамів води, що міститься в деревині, припадає на 100 г абсолютно сухої деревини. Наприклад, вологість деревини 20 %. Це означає, що на кожні 100 г цієї деревини в абсолютно сухому стані припадає 20 г наявної в ній води; 100 г абсолютно сухої деревини при вологості 20 % важить 120 г.
За ступенем вологості розрізняють такі види деревини: мокра, яка тривалий час перебувала у воді (понад 100 %); свіжозрубана (50 – 100 %); повітряно-суха, що довго зберігалась на повітрі (15 – 20 %); кімнатно-суха (8 – 12 % ) і абсолютно суха (0 %). За умовну стандартну вологість прийнято брати вологість деревини, що становить 12 %.
При виборі матеріалу потрібно враховувати, що суха деревина більш гігроскопічна, а отже поглинатиме більше вологи з навколишнього середовища, унаслідок чого збільшиться в розмірах (розбухне). Але з іншого боку, якщо матеріал свіжозрубаний, у процесі висихання він зменшиться в розмірах, можуть з’явитися тріщини (це явище називають усиханням деревини). Крім того, внаслідок нерівномірного висихання різних шарів (з поверхневих шарів вода випаровується швидше) деревина коробиться, тобто деформується, нерідко з появою тріщин. Під час усихання чи набухання зміна лінійних розмірів є більш значною упоперек волокон і може становити до 5-8 % від початкових розмірів. Використання різноманітних покриттів дозволяє значно зменшити гігроскопічність деревини.
Щільність – це відношення маси деревини за певної вологості (кг), до її об'єму (м3). Деревину з більшою щільністю (бук, клен, граб, груша) особливо цінять за її міцність. Деревина хвойних порід має меншу щільність, ніж листяні породи. Тому її важче лакувати і полірувати.
Міцність – це здатність деревини чинити опір руйнуванню під дією механічних навантажень. Міцність зменшується при збільшенні вологості та наявності дефектів (вад). Цю властивість потрібно враховувати для виробів, у яких конструкція несе значні механічні навантаження (наприклад, ніжки у стола, перекладини у драбини).
Твердість – це здатність деревини чинити опір проникненню в неї більш твердого тіла. Різальні інструменти для обробки деревини добирають і заточують з урахуванням її твердості. За ступенем твердості всі деревні породи можна розділити на три групи: м'які (ялина, сосна, кедр, ялиця, тополя, липа, осика, вільха); тверді (модрина сибірська, береза, бук, дуб, в'яз, клен, ліщина, горіх, яблуня, ясен); дуже тверді (акація біла, береза залізна, граб, кизил).
Деревина як конструкційний матеріал має певні технологічні властивості, зокрема: здатність утримувати металеві кріплення, здатність до згинання, зносостійкість і опір розколюванню.
Властивість деревини утримувати в собі металеві кріплення(цвяхи, нагелі, шурупи та ін.) пояснюється її пружністю. Цвях, що забивають у деревину, розсовує волокна, які внаслідок своєї пружності тиснуть на поверхню цвяха і тим самим чинять опір його витягуванню.
Сила утримування цвяхів і шурупів у деревині залежить від площі дотикання забитої частини цвяха до деревини й глибини загвинчування різьби шурупа в деревину.
Зносостійкість – це здатність деревини чинити опір зношуванню, тобто поступовому руйнуванню її поверхні при терті. Зношування бічних поверхонь більше, ніж торцевих; зношування вологої деревини більше, ніж сухої.
Визначити фізико-механічні та технологічні властивості деревини без лабораторного обладнання досить складно. Але ці властивості є характерними для різних порід деревини і описані у спеціальній літературі. Наприклад, липа – м’яка порода, а дуб – тверда. Розглянемо важливі характеристики поширених порід,які потрібно враховувати при виборі деревини для виготовлення виробу.
Сосна.Деревина неоднорідна, помірно міцна, легка і м'яка. Сосна добре обробляється різальним інструментом. Деревина сосни смоляниста, погано вбирає воду і тому не загниває, не жолобиться, добре зберігається за різних кліматичних умов.
Ялина. Деревина неоднорідна, помірно міцна, м'яка, легка, крихка. За своєю текстурою, фізичними та механічними властивостями нагадує сосну, але менш смоляниста. Ялина має істотний недолік – швидко гниє у вологому середовищі.
Деревина хвойних порід досить складно шліфується.
Вільха.Деревина м'яка, при всиханні майже не зменшується в об'ємі і практично не розтріскується. Має перевагу перед іншими породами, бо у воді набуває особливої стійкості за рахунок наявності дубильних речовин. Завдяки однорідній будові використовується для виготовлення токарних і різьблених виробів, скульптур, посуду, меблів.
Липа.Деревина однорідна, м'яка, легка, щільна, легко піддається різанню та токарній обробці, мало розтріскується і сильно всихає. З липи виготовляють скульптур, меблі, культові вироби (іконостаси), посуд, обладнання, іграшки, ложки, високохудожні вироби і прикраси. Вироби з деревини цієї породи потребують сухого приміщення, щоб запобігти жолобленню, гниттю та іншим пошкодженням.
Осика.Надзвичайно цінна порода, легка, м'яка, еластична, легко вбирає вологу, однорідної структури. Деревина осики добре колеться, ріжеться, полірується, помірно всихає, мало жолобиться. Осика – чудовий матеріал для токарства, виготовлення бондарського посуду, різьблених виробів, скульптур, меблів тощо.
Береза.Завдяки однорідній будові тверда і важка деревина берези добре обробляється й імітується під цінні породи (червоне і чорне дерево). До її недоліків слід віднести невелику стійкість проти гниття і жолоблення. Деревину берези широко використовують для виготовлення меблів, бондарного посуду, токарних виробів, дитячих іграшок, різноманітних художніх виробів.
Дуб.За твердістю, щільністю і міцністю займає перше місце,дуже стійкий проти загнивання. Важко піддається різанню і шліфуванню, крім того, при висиханні утворюється значна кількість тріщин. З дуба виготовляють різні меблі, паркет, фанеру, шпон, довбані та точені, а також столярні вироби, посуд, скульптур, різьблені та токарні художні вироби.
Одним із суттєвих недоліків деревини як конструкційного матеріалу є наявність досить значної кількості природних вад, які потрібно знати й ураховувати в процесі виготовлення виробу. Вони часто ускладнюють роботу, а інколи роблять деревину непридатною до використання.
Вадами вважають недоліки окремих ділянок деревини, які знижують її якість і можливості використання. Це сучки, тріщини, вади форми стовбура, вади будови дерева, хімічні забарвлення, грибкові ураження, пошкодження комахами.
Приклади вад деревини, які зустрічаються найчастіше, наведені у таблиці 4.2.
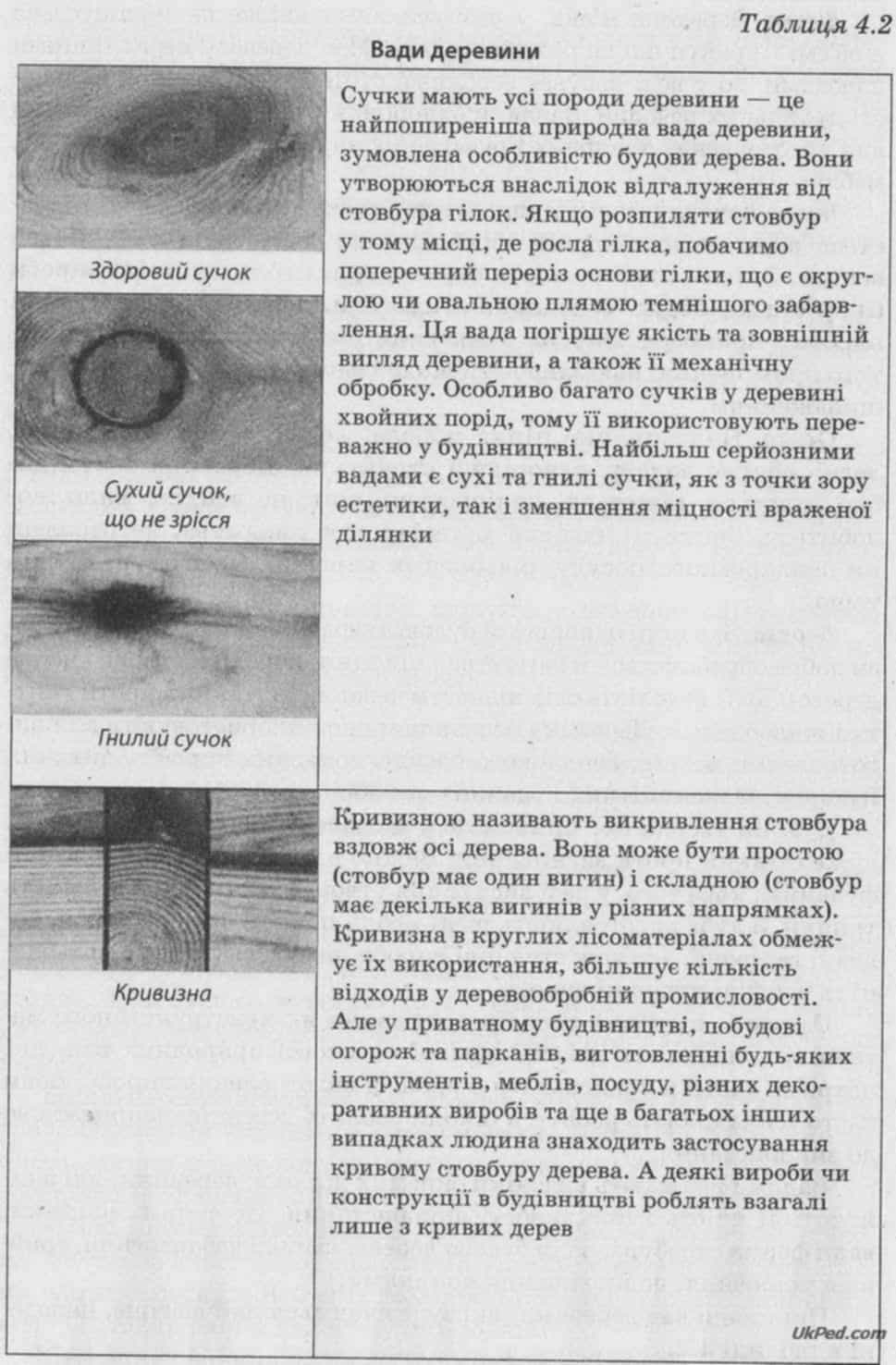
Тема 4.2. Процес розмічання заготовок із деревини
Послідовність виготовлення виробу. Інструменти для розмічання.
Прийоми вимірювання заготовок із пиломатеріалів та їх розмічання. Припуски на обробку пиломатеріалів. Економне використання матеріалів.
Послідовність виготовлення виробу, як правило, складається з таких етапів: підбір матеріалу, інструментів, обладнання, пристосувань; вибір заготовок; розмічання деталей; виготовлення деталей; монтаж виробу; оздоблення; опорядження. Залежно від конструкції виробу, техніки його оздоблення тощо порядок виконання цих етапів може бути змінений, а деякі операції взагалі не виконують.
Попередню розмітку дощок на чорнові заготовки або деталі (перший етап) виконують із припусками на стругання, обраними згідно зі стандартами. Припуски слід вибирати оптимальні, оскільки надто великі призводять до перевитрат пиломатеріалів і для їх обробки витрачається значно більше часу і сили. Залежно від розмірів брускових деталей припуски становлять від 1,5-7,0 мм (за шириною і товщиною) і до 20 мм (за довжиною).
Попередню розмітку пиломатеріалів на чорнові заготовки роблять за допомогою метра, рулетки, лінійки і кутника. Лінії наносять олівцем.
Другим етапом є розмічання основних з’єднувальних елементів, що виконують на деталях, які мають правильну форму (вистругані за розмірами, зазначеними на кресленні).
Для розмічання основних з'єднувальних елементів (шипів, провушин, гнізд тощо) і контролю процесу їх виготовлення застосовують різноманітний розмічальний і контролюючий інструмент, а також шаблони і спеціальні пристрої (мал. 4.5).
Єрунок (мал. 4.5, б) є одним з різновидів кутника, тільки його лінійка перебуває під кутом 45° і 135° до колодки. Ним користуються при розмічанні з’єднувальних елементів під кутом 45° (на «вус»).
Малка (мал. 4.5, в) також є різновидом кутника, тільки лінійка з колодкою з’єднані шарнірно, що дає змогу розмічати і перевіряти будь-які кути.
Рейсмус – це лише розмічальний інструмент (мал. 4.5, г). Він складається з колодки і двох висувних брусків (штанг), закріплених клинком. На кінці брусків є металеві штифти, якими й прокреслюють лінії на деталях. Проте звичайний рейсмус не дає можливості проводити риски на відстані понад 100–150 мм від ребра деталі, тому для проведення рисок на більшій відстані застосовують щитовий рейсмус. Якщо на брускових деталях потрібно провести більше ніж дві паралельні лінії (при виготовленні групових шипів), то раціональніше застосовувати замість рейсмуса розмічальну гребінку.
Діаметр круглих деталей перевіряють кронциркулем (мал. 4.5, є). Нутроміром визначають діаметри отворів та ширину гнізд (мал. 4.5, ж). Обидва ці інструменти може замінити штангенциркуль, яким вимірюють зовнішні та внутрішні розміри.
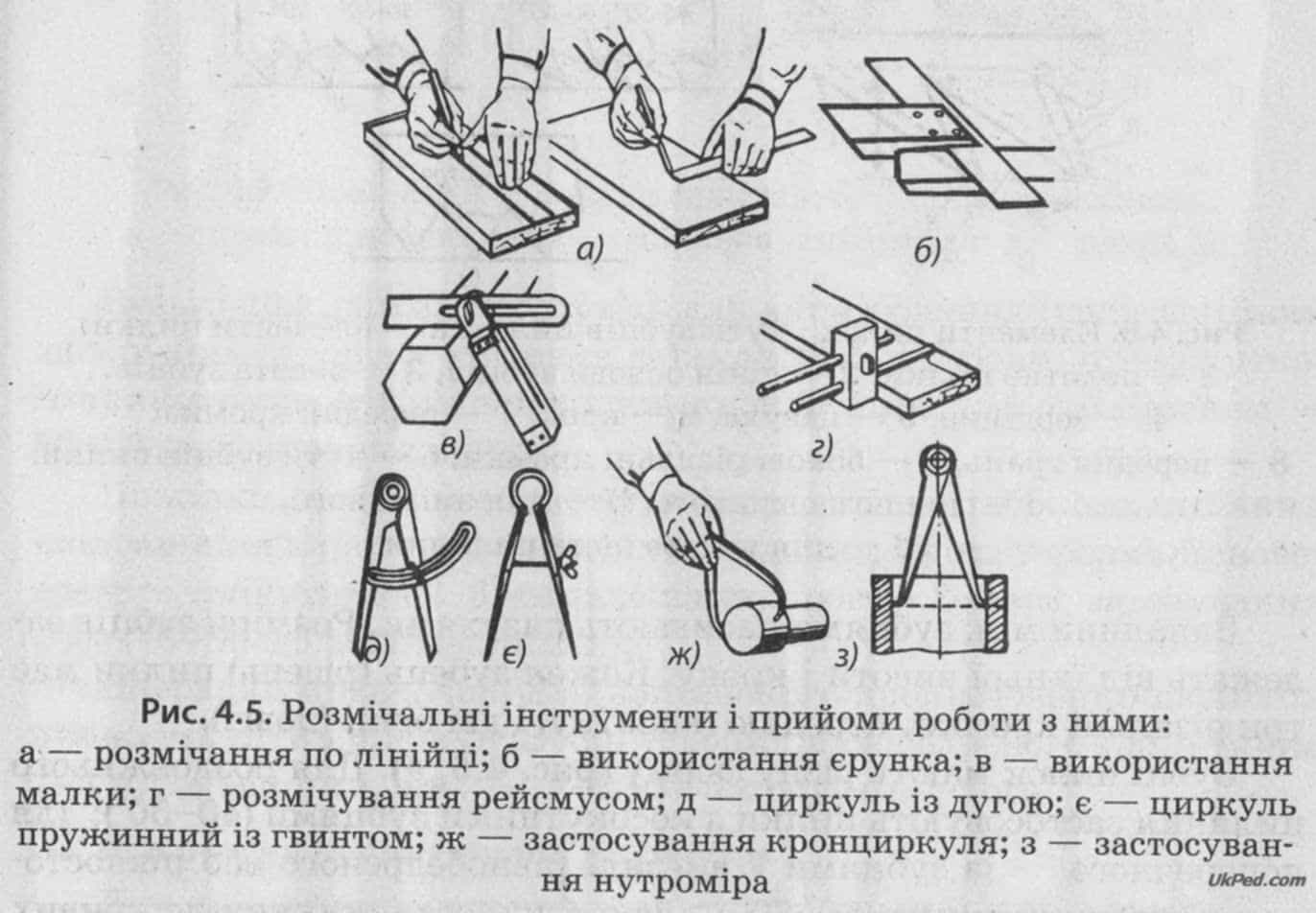
Тема 4.3. Процес пиляння деревини
Інструменти для пиляння деревини. Будова ножівки. Форма зубців ножівки. Розведення та заточування зубців. Пиляння вздовж і впоперек волокон. Припуски на пиляння. Прийоми запилювання. Стусло та його застосування.
Пиляння – це процес закритого різання, що здійснюється багаторізцевими інструментами – пилками. Пилянням здійснюють розкрій матеріалів на заготовки, торцювання деталей по довжині, розкрій щитів плитових матеріалів фанери, обпилювання кромок щитів і рамок, випилювання криволінійних заготовок, а також запилювання шипів і провушин.
Пилка (мал. 4.6, а) – це металева пластина з нарізаними на ній з одного боку зубцями. Цей бік пилки називають зубчастим вінцем. Кромка, протилежна зубчастому вінцю, називається спинкою, а бокові стінки – щічками. Лінія, де зубець бере початок, називається основою, а кінець зубця, що закінчується передньою кромкою,– вершиною. Відстань від основи до вершини називають висотою зубця і позначають буквою h, а відстань між двома суміжними зубцями називають кроком і позначають буквою t.
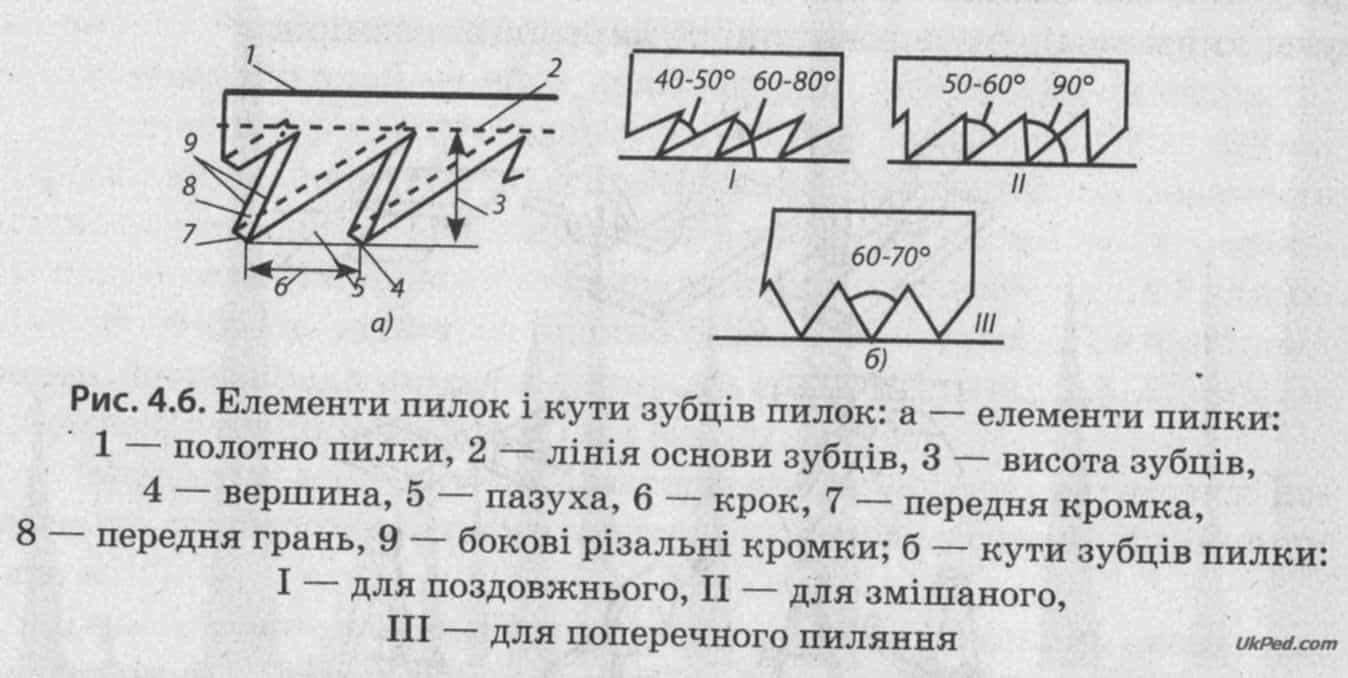
Западини між зубцями називають пазухами. Розміри зубців залежать від їх висоти і кроку. Кожен зубець (різень) пилки має три різальні кромки: передню (коротку) і дві бічні (довгі).
Зубці пилок мають різну форму (мал. 4.6, б). Для поздовжнього пиляння застосовують пилки з косокутними зубцями (40–50°); для поперечного – із зубцями у вигляді рівнобедреного або рівностороннього трикутника (60–70°); для змішаного (пиляння по кривих лініях) – із зубцями у вигляді прямокутного трикутника (50–60°). Чим твердіша деревина, тим більший потрібен кут загострення. Під час різання пилками в пропилі утворюється тирса, що скупчується в пазухах зубців. У процесі різання деревини м'яких порід пазухи і кроки завжди більші, ніж при різанні твердих порід, бо за робочий хід пилки в м'якій породі знімається значно більше деревини.
Залежно від виду різання застосовують такі кути різання: для поздовжнього – до 80°, для змішаного – до 90°, для поперечного – понад 90°.
Ручні столярні пилки.За конструкцією ручні столярні пилки поділяють на натягнуті (лучкові) і ненатягнуті (ножівки і наградки). Ножівки бувають різних видів (мал. 4.7).
Широкі ножівки застосовують для розкрою широких дощок і плитових матеріалів. Зубці мають форму рівнобедреного або прямокутного трикутника, 3–6 мм заввишки, крок – 4 - 6 мм, кути різання і заточування в цих пилках аналогічні й залежать від форми зубців.
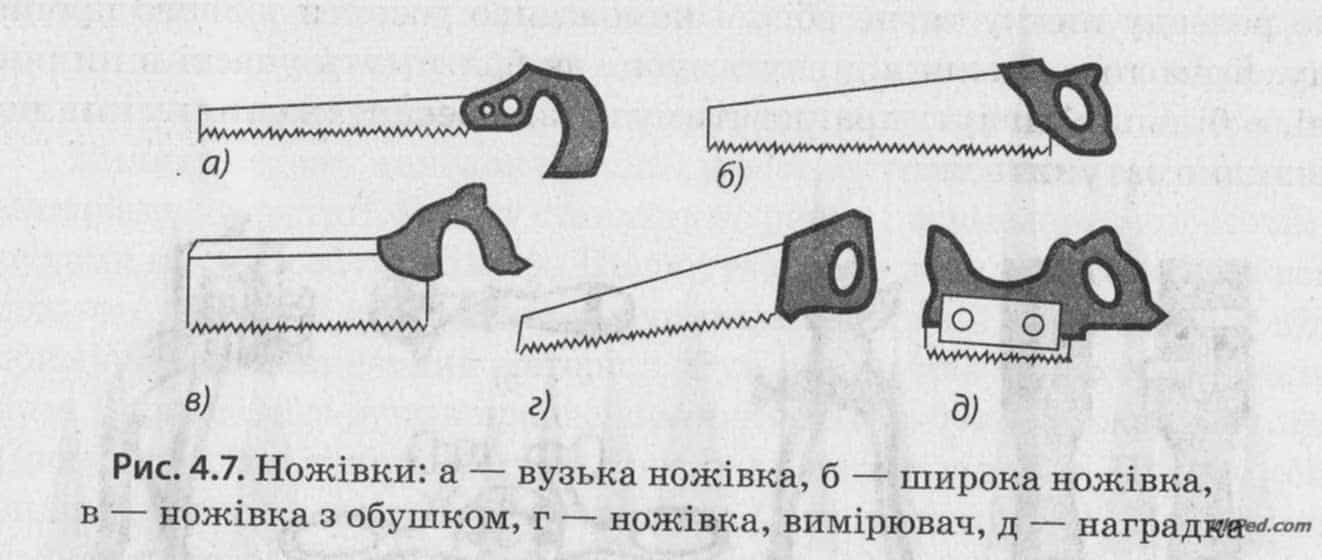
Вузькі ножівки застосовують для випилювання криволінійних наскрізних отворів у щитових деталях. Зубці у формі прямокутного трикутника 2 - 4 мм заввишки, крок 3 - 4 мм, кут загострення – 50 - 80°, заточування пряме.
Ножівки з обушком застосовують для неглибокого пиляння і підганяння виробів у процесі їх складання. Зубці у формі рівнобедреного трикутника 2 - 3 мм заввишки, крок – 2 - 3 мм, заточування косе (75 - 80° до полотна пилки).
Наградки призначені для неглибокого пропилювання пазів під вузькі шпунти і шпонки. Зубці у формі рівнобедреного трикутника 2 - 3 мм заввишки, крок – 2 - 3 мм, заточування косе.
Підготовка ручних пилок до роботи
Для забезпечення високопродуктивної праці й відповідної якості деталей пилки треба добре налагодити і нагострити. Перед налагодженням полотно пилки слід очистити від бруду, іржі й смоляного нальоту ганчіркою, змоченою в гасі. Спочатку вирівнюють полотно пилки легкими ударами на рівній чавунній або стальній плиті. Вирівнювати його можна і в лещатах з мідними або алюмінієвими пластинками: легенько затиснувши між ними полотно пилки, протягують його. Після вирівнювання прорізають напилком між зубцями пазухи і вирівнюють профіль і висоту зубців, тобто їх фугують. Для фугування застосовують спеціальний пристрій, який складається з дерев'яної колодки з проріззю для полотна пилки і круглого отвору, куди вставляють тригранний напилок. Цей пристрій рухають по зубцях пилки (або навпаки), вирівнюючи вершини зубців пилки по висоті.
Для полегшення ходу пилки в пропилі, а також для зменшення витрат сили на різання, її зубці розводять спеціальними розводками (мал. 4.8). При цьому спочатку відгинають одну половину зубців в один бік через один зубець, а другу – в протилежний. Величина розводу всіх зубців пилки має бути однаковою. У разі неоднакового розводу пилку тягне вбік, і неможливо досягти рівного пропилу. Крім того, менш відігнуті зубці не братимуть участі в пилянні, а більш відігнуті працюватимуть із перевантаженням, і пилка швидко затупиться.
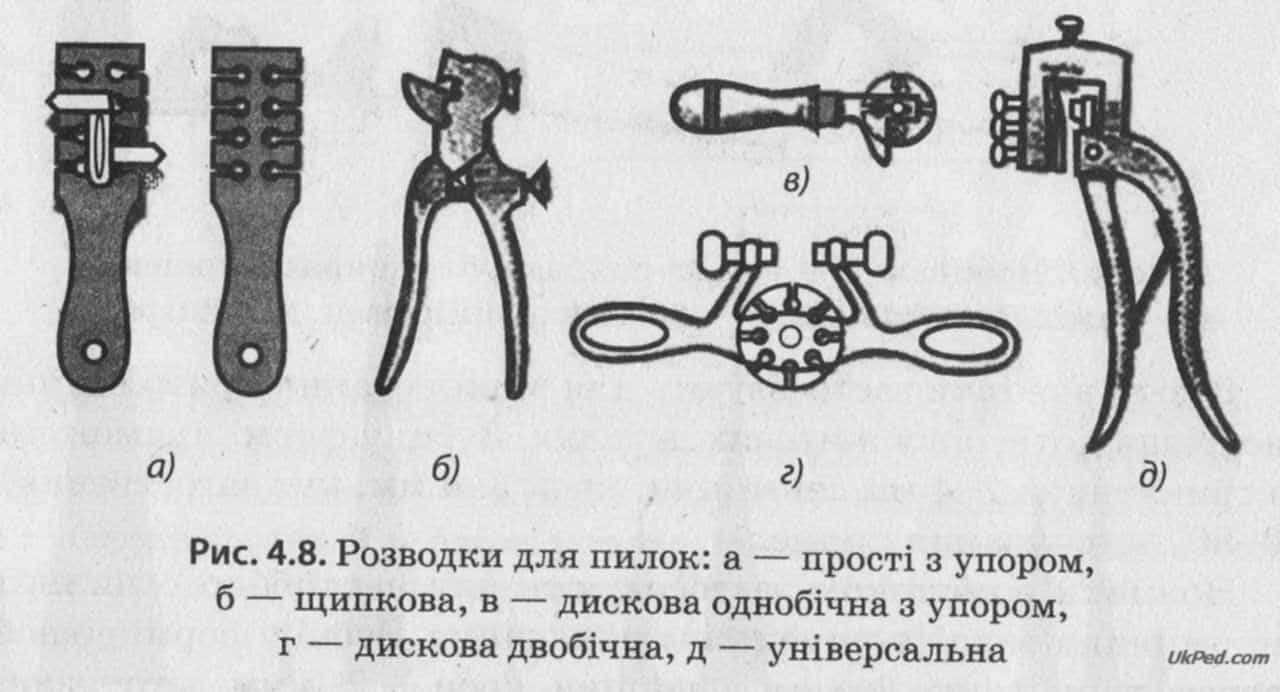
Після розводу пилку загострюють тригранним або ромбічним напилком з дрібною насічкою. Для заточування полотна пилку затискають у лещата, як і при розводі. Гострять пилку через зубець: спочатку проходять напилком з одного боку пилки, потім її повертають другим боком до себе і гострять пропущені зубці. Натискати треба рівномірно і несильно, бо від сильного натискання утворюються великі задирки і пилка нагрівається. При зворотному русі (на себе) напилок трохи піднімають.
Прийоми пиляння ручними пилками
Перед тим, як почати пиляння ручними пилками, роблять попередню розмітку. Щоб пропил не відхилявся від риски, за її напрямом до полотна пилки прикладають ніготь або суглоб великого пальця. Для безпеки їх прикладають вище від зубців. Запил роблять плавними рухами пилки до себе. Після утворення невеликого заглиблення (пропилу) пилкою рухають рівномірно, але вже швидше (60–80 разів за хвилину). При допилюванні відрізка дошки чи бруска його слід підтримувати лівою рукою, сповільнивши при цьому рух пилки, щоб не обламався кінець дошки і не утворився при цьому відкол.
При поздовжньому пилянні дошку або брусок кладуть горизонтально на верстат і закріплюють струбциною так, щоб відпилювана частина звисала з верстата. Пилку тримають вертикально правою рукою за ручку, а лівою – за кінець стояка. Пиляють трохи натискуючи на пилку при русі її вниз; при холостому русі пилки вгору зубці пилки відводять від дна пропилу. При затискуванні пилки стінками пропилу в нього вставляють клинок. Для розпилювання довгих дощок уздовж волокон застосовують верстатні підставки.
Пиляти вздовж волокон можна і при вертикальному закріпленні матеріалу у верстаті. Пилку ставлять на риску і повільними короткими рухами до себе роблять запил. Після утворення запилу пиляють на всю довжину полотна пилки, тримаючи пилку в правій руці, а лівою підтримують розпилюваний матеріал. Рух пилки має бути горизонтальним. Корпус і ліва рука в процесі пиляння мають бути майже нерухомі. Процес різання відбувається при русі пилки від себе. При всіх видах пиляння натиск на полотно має бути рівномірним. Надмірний натиск призводить до скривлення пропилу, а іноді й до полому пилки.
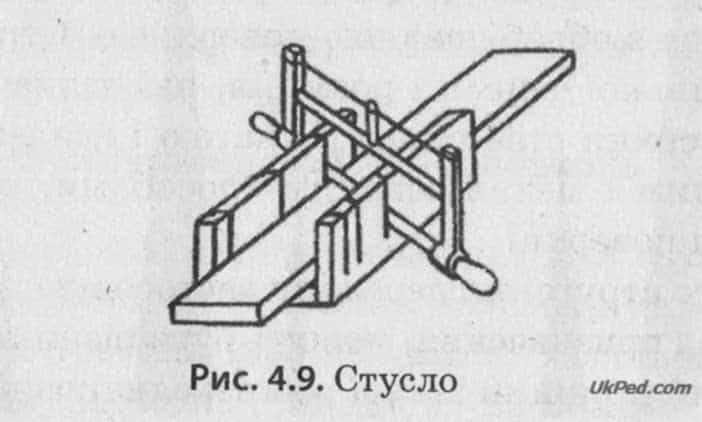
Стусло – це важливий інструмент, необхідний для проведення точних робіт із деревообробки. Стусло – це пристосування, яке служить для виробництва розпилів з фіксованим кутом. Найпростіше стусло – це дерев’яний лоток, у бічних стінках якого зроблені пропили під заданими кутами (мал. 4.9).
Принцип дії такого стусла досить простий: брус або дошка, котрі потрібно розпиляти під заданим кутом, кладуться в лоток для розпилу. Потім за допомогою простої ручної пилки розпилюємо брус, за лінією, заданої пропилом в стінці лотка. Так брус розділяється на дві частини під заданим кутом.
На сьогодні більшою популярністю користується поворотне стусло, яке дозволяє самостійно задавати потрібний кут розпилу, точність якого доходить до мінімальних траєкторій. Поворотне стусло має пристрій, який дозволяє зафіксувати заготовку. Заготовка розпилюється ножівковим полотном, у якому задається кут за допомогою спеціальних позначень і фіксатора.
Найбільш сучасне і технологічне стусло – це електричне. Його можна порівняти з електропилкою, де є опція визначення кута нахилу самої пилки. Зазвичай, електричне стусло – це конструкція, що складається зі столу з зручними опорами для дощок і цифровими індикаторами, які дозволяють найбільш точно встановлювати кут розпилу. Деякі моделі електричного стусла оснащуються лазерною розміткою, яка робить процес розпилювання практично досконалим. Саме у високій точності, великій швидкості обробки деревини і полягає основна перевага цього інструмента.
Тема 4.4. Процес стругання деревини
Технологічний процес стругання деревини. Поняття про утворення стружки. Інструмент для стругання (рубанок, шерхебель). Підготовка рубанка до роботи. Прийоми стругання фаски, крайки, пласті. Перевірка якості стругання (на просвіт).
Стругання деревини ручними інструментами
Струганням називають процес різання, при якому площина різання збігається з оброблюваною поверхнею. Струганням надають деталям правильної форми і розмірів, які зазначені на кресленні. Крім того, поверхня стає рівною, чистою і гладенькою. Стругають деревину ручним і механізованим способами, отримуючи плоскі й криволінійні поверхні.
Для ручного стругання деревини застосовують рубанки (струги), які, залежно від призначення, можуть бути різними за конструкцією, проте загальний принцип їхньої роботи однаковий.
Розглянемо будову одного з найбільш поширених рубанків (мал. 4.10). Він складається з дерев'яної колодки і клинка, виготовлених із деревини граба, бука, ясеня, груші, та зі стального ножа з гострим лезом, закріпленого в колодці за допомогою клинка.
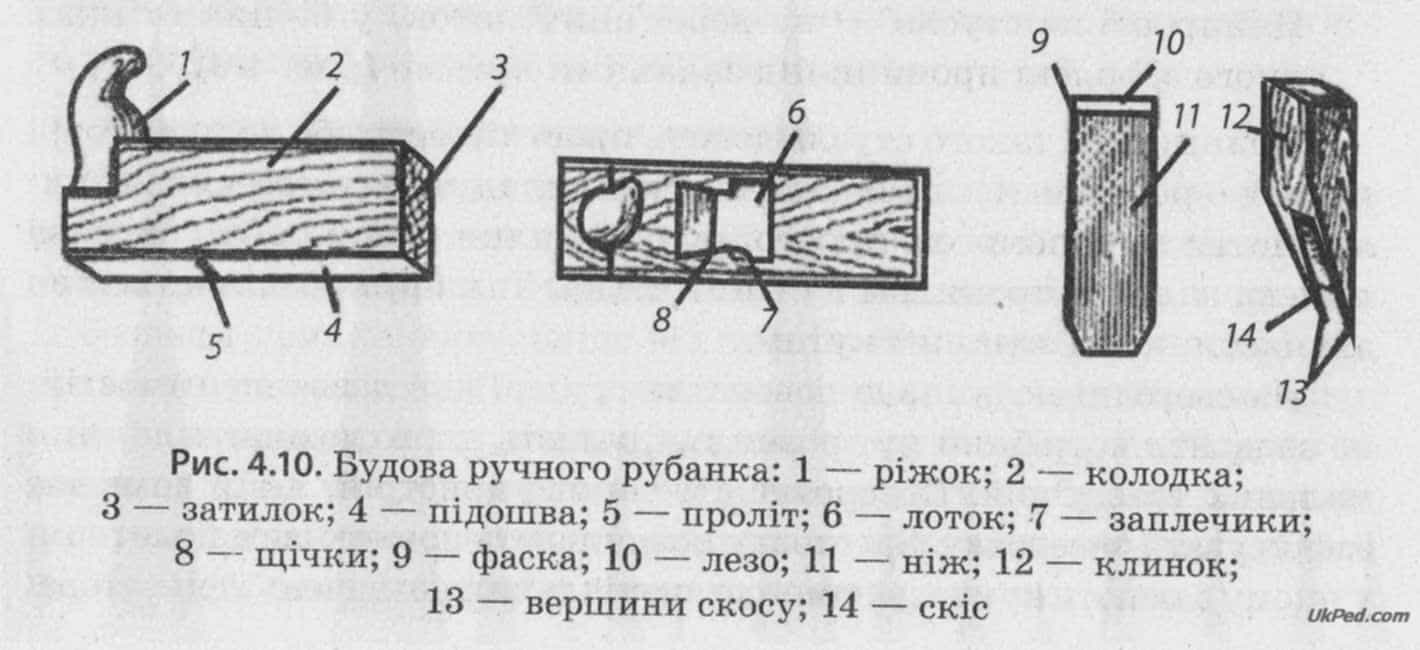
Нижня частина колодки називається підошвою. Вона має бути плоскою для стругання плоских поверхонь або мати зворотний профіль оброблюваної поверхні при криволінійних і профільних поверхнях. Для встановлення ножа і виходу стружки в колодці продовбане гніздо (лоток), що звужується до виходу з підошви до ширини 5 - 9 мм (проліт). Чим проліт вужчий, тим чистішою виходить поверхня стругання. Якщо підошва стирається і проліт розширюється, то в передню частину її вставляють на клей п'ятикутну вставку з твердої породи деревини (самшиту, груші, граба). Цим вирівнюють передню частину прольоту і роблять його вужчим.
Задня частина прольоту утворюється внаслідок перетину задньої частини лотка з підошвою. Кут, утворений між ними, називають кутом присадки ножа, і він завжди дорівнює куту різання. Ніж має щільно прилягати до площини лотка, щоб у процесі стругання не виникало вібрації. Кріпиться ніж за допомогою клинка, який упирається в бокові заплечики на бокових стінках лотка. Ножі виготовляють із високоякісної інструментальної вуглецевої термічно обробленої сталі, леза загартовують.
Інструменти для стругання плоских поверхонь
Шерхебель (мал. 4.11, а) застосовується для грубого стругання заготовок уздовж волокон або під деяким кутом, особливо коли треба зняти товстий шар деревини. Різальна кромка ножа має овальну форму і виступає з підошви на 2–3 мм. Це дає можливість знімати товсту стружку без значних зусиль і без виривів деревини з боків різця ножа. Однак на виструганій поверхні залишаються жолобкуваті нерівності, які знімають іншими рубанками.
Одинарний рубанок (мал. 4.11, б) служить для вирівнювання поверхні після стругання шерхебелем або після розпилювання матеріалу. Різальна кромка його ножа пряма і тільки у кутах трохи заокруглена для того, щоб запобігти задирам при струганні деревини. Після стругання одинарним рубанком поверхня стає рівною, але недостатньо гладенькою.
Подвійний рубанок (мал.4.11, в) використовується для зачищення поверхонь і стругання торців. Він робить поверхню гладенькою завдяки тому, що його ніж складається з двох частин:
основний ніж такий же, як і в одинарного рубанка, але він має проріз для кріплення другого ножа, який називається стружколомом. Стружколом ставлять на передню грань основного ножа так,
щоб їхні кромки були паралельні, а відстань від кромки стружколома до леза різця становила 0,5–1 мм. Чим ближче лезо стружколома до леза різця, тим тонша стружка, а, отже, й рівніша поверхня.
Проте подвійним рубанком можна вирівнювати тільки короткі деталі.
Підготовка ручних рубанків до роботи
Для якісного стругання треба добре нагострити і правильно налагодити інструменти. Щоб нагострити ніж, його виймають із лотка, притримуючи великим пальцем,
і ударяють киянкою по затилку колодки (мал.4.12) в фуганку легкими ударами по кнопці. Заточують ніж на точилі з природного каменю або на наждачному крузі до утворення
задирів на передній грані ножа. Правлять ніж на бруску коловими рухами. Кут загострення перевіряють шаблоном, а правильність заточування леза – кутником і лінійкою.
Нагострений ніж ставлять у лоток колодки і закріплюють дерев'яним клинком. Клинок має бути добре підігнаний і щільно притискати
Домашнє завдання. Опрацювавши теоретичний матеріал, у зошитах зробіть, будь ласка, стислий конспект.
Фото відповідей надсилайте у вайбер 099-63-72-507
або на ел. пошту marinalutay84@gmail.com
6.05.2020р. Створення банку ідей, пошук моделей-аналогів. Матеріали хімічного походження. Добір матеріалів, інструментів та технологій для виконання проекту(2 академічні години)
«Хто володіє інформацією, той володіє світом», – сказав
колись Уїнстон Черчілль. Проте,
варто доповнити цю фразу. Хто володіє інформацією та вміє нею користуватися –
той володіє світом.
Способи пошуку інформації в пошукових сервісах:
Простий пошук (пошук за одним словом)
Розширений пошук (використовують спеціальні форми, за допомогою яких
виконується розширений пошук. Можна сконструювати запит так, що будуть знайдені сайти, сторінки
й окремі документи)
Контекстний пошук (на відкритій у браузері сторінці слід виділити фрагмент
тексту. Система проаналізує виділений текст, виділить ключові слова й сама
складе пошуковий запит)
Спеціальний пошук (Дозволяє виконати пошук документів за датами, за
посиланнями на певну адресу, за заголовками Web-сторінок)
Матеріали хімічного походження
Виготовлення будь-яких виробів не можливе без певних матеріалів, які називаються конструкційними.
Існують матеріали, виготовлені із сировини природного походження: деревина, метали, тканини тощо. Під впливом сонячного проміння, коливань вологи, зміни температур, під дією великого тиску чи навантаження природні матеріали можуть псуватися. Тому конструктори та технологи шукають шляхи покращення якостей таких матеріалів: деревину фарбують або лакують, метал покривають захисними плівками, при виготовленні скла, щоб зробити його міцнішим, використовують металевий сітковий каркас.
Для виготовлення одягу й різних виробів домашнього вжитку людина довгий час використовувала тільки природні волокнисті матеріали.
Зі збільшенням кількості людства зростають потреби населення в тканинах і гостро посідає проблема нестачі волокнистих матеріалів. Людина не має можливості задовольнити ці потреби шляхом розширення площ для промислового вирощування волокон та пасовищ для тварин. Тому виникла потреба в отриманні волокон іншим способом — хімічним.
Способи отримання штучних та синтетичних матеріалів
Виготовлення хімічних волокон відбувається двома шляхами:
1. До природної сировини — деревини, відходів бавовни тощо — додають певні хімічні речовини.
2. Як початкову сировину для виробництва синтетичних волокон використовують природний газ, продукти переробки кам’яного вугілля та нафти.
Волокна, які одержують переробкою природних матеріалів, називають штучними, а ті, що одержують із синтезованих полімерів,— синтетичними.
Класифікація матеріалів хімічного походження. Переваги й недоліки штучних та синтетичних матеріалів у порівнянні із натуральними матеріалами
Нагадую вам етапи проектної діяльності
Назва етапу
| Зміст роботи |
Обґрунтування проекту | Формулювання мети й завдання проекту, обґрунтування його соціальної значущості, визначення теми проекту; організація робочих груп, розподіл завдань між учасниками проекту |
Пошуковий | Дослідження проблеми й збір інформації (визначення кола джерел та пошук необхідних відомостей; аналіз можливих варіантів вирішення проблеми); вибір оптимального варіанта виконання проектного завдання (генерування ідеї); розроблення плану роботи над проектним завданням; добір матеріалів та інструментів; вибір форми презентації результатів проекту |
Технологічний | Здійснення діяльності кожного учасника проекту згідно з планом роботи над проектним завданням (реалізація проекту); підготовка презентації результатів проекту |
Заключний | Проведення презентації (захист проекту) оцінка результатів виконання проекту, колективних і особистих досягнень учасників проекту |
Домашнє завдання. Оберіть, будь ласка, виріб, який би ви хотіли виготовити і постарайтеся розписати в зошиті послідовність виготовлення цього виробу
Фото відповідей надсилайте у вайбер 099-63-72-507
або на ел. пошту marinalutay84@gmail.com
29.04.2020р. Визначення завдання та плану проектної діяльності (2 академічні години)
Дорогі учні! Тему проектів ви почали вивчати ще у 6 та 7 класах з Дмитром Володимировичем. Саме тому, сподіваюся, вам буде нескладно. Ознайомтеся з теоретичним матеріалом і оберіть, який виріб ви б хотіли зробити. Це й буде домашнім завданням.
Метод проектів надає величезний простір для реалізації ваших ідей. Існує кілька видів проектів, і ви можете вибрати той, що вам найбільше подобається. З матеріалів, зібраних на кожному етапі проектування, необхідно комплектувати портфоліо проекту. Вибравши тему свого проекту, необхідно відразу обміркувати вид продукту й вид презентації цього продукту.
Види проектів:
♦ практично орієнтований проект спрямований на рішення соціальних завдань, що відображають інтереси учасників проекту або інших осіб (розробка моделей сучасного молодіжного одягу, складання меню тематичного вечора-банкету, розробка й виготовлення меблів тощо);
♦ дослідницький проект — це варіант наукового дослідження (вивчення історії костюма). Такі проекти оформлюються у вигляді рефератів, доповідей, Web-сайтів, альбомів, енциклопедій тощо;
♦ інформаційний проект — це проект, що спрямований на збір інформації про який-небудь об'єкт або з певної теми з метою аналізу, узагальнення й уявлення інформації для широкої аудиторії (маркетингові дослідження, соціологічне опитування). Ці проекти оформлюються у вигляді каталогів, буклетів, питальників, інформаційних стендів, рекламної продукції— це проект, що розігрується за самостійно створеним сценарієм (проблемно-рольові ситуації, основані на сучасному матеріалі, аналоги телепередач, наприклад «Модний вирок», «Очумілі ручки» тощо);
♦ творчий проект — це проект, що припускає вільний і часом нетрадиційний підхід до його виконання й до презентації результатів (показ мод, відеофільм, вистава тощо).
Етапи проекту
Назва етапу
| Зміст роботи |
Обґрунтування проекту | Формулювання мети й завдання проекту, обґрунтування його соціальної значущості, визначення теми проекту; організація робочих груп, розподіл завдань між учасниками проекту |
Пошуковий | Дослідження проблеми й збір інформації (визначення кола джерел та пошук необхідних відомостей; аналіз можливих варіантів вирішення проблеми); вибір оптимального варіанта виконання проектного завдання (генерування ідеї); розроблення плану роботи над проектним завданням; добір матеріалів та інструментів; вибір форми презентації результатів проекту |
Технологічний | Здійснення діяльності кожного учасника проекту згідно з планом роботи над проектним завданням (реалізація проекту); підготовка презентації результатів проекту |
Заключний | Проведення презентації (захист проекту) оцінка результатів виконання проекту, колективних і особистих досягнень учасників проекту |
Проектування - процес, який
починається з моменту отримання завдання; розробка концепції, аналіз
об’єкта, конструювання, макетування, проектна документація:
- назва об’єкта;
- функція, призначення;
- габаритні розміри;
- аналіз існуючих аналогів ( матеріал, форма,
естетика…)
- вимоги до дизайну об’єкта;
- норми витрати матеріалу;
- ескізи креслення виробу;
Базова модель – форма виробу, яку
використовують для розробки цілого ряду подібних виробів.
Модель – аналог – це модель, що створена на основі базової моделі,
але відрізняється формою деталей чи оздобленням.
Проектною роботою може бути виготовлення рамки для фото, годівнички для птахів, підставки під гаджет, пенопластові макети літаків тощо.
22.04.2020р. Тема: Технологія ручної обробки деревинних матеріалів (2 академічні години)
Добрий день, дорогі учні! Ознайомтеся з теоретичним матеріалом та перегляньте, будь ласка, цікаві відео:
https://www.youtube.com/watch?v=HgLMmrjJzwI Кушницький "Мікеланджело" бензопилою вирізає дерев‘яні шедеври
https://www.youtube.com/watch?v=bD4SR_YjhEQ Меблі з дерева. Майстри ручної роботи
Сьогодні це й буде вашим домашнім завданням.
У господарстві, промисловості й у побуті широко застосовується клеєна і стругана фанера.
Саме слово "фанера" прийшло до нас з німецької мови (нім. Furnier – шпон, фанера; від франц. Fournir – постачати, накладати). Клеєна фанера складається з трьох або більше листів шпону, склеєних між собою так, щоб напрямок волокон у них був взаємно перпендикулярним.
Лущеним шпоном називають тонкий шар деревини товщиною від 0,3 до 2 мм. Шпон виготовляють на спеціальних лущильних верстатах із деревини берези, вільхи, клена, бука, сосни, ялини, модрини. Розпарену коротку колоду встановлюють у верстат і приводять у рух. До колоди підводять довгий ніж із притискачем. При цьому колода розгортається як рулон паперу. Потім рулон шпону розрубують на окремі листи на спеціальному верстаті.
Листи шпону після просушки промазують тонким шаром клею і склеюють у гарячих гідравлічних пресах. Склеєні пакети фанери розрізають за стандартними розмірами.
Струганий шпон – це тоненькі листи, отримані шляхом стругання брусів із деревини, що має красиву текстуру (дуб, бук, горіх, клен, ясен, червоне дерево). Операція здійснюється на шпонострогальних верстатах. Використовується струганий шпон для облицювання виробів із деревини і деревних напівфабрикатів під час виготовлення меблів.
Фанеру виготовляють шляхом склеювання трьох і більше шарів лущеного шпону. Сусідні аркуші розташовуються так, щоб напрямок волокон у них був взаємно перпендикулярним. Завдяки перехресному напряму волокон фанера відрізняється від інших листових матеріалів порівняною однорідністю фізико-механічних властивостей, а також менше коробиться і розтріскується у різних умовах експлуатації. Звичайна тришарова фанера є хорошим і доступним матеріалом для виготовлення художніх виробів. Найкращою вважається березова та ясенева фанера вищих сортів.
Перевага фанери перед іншими матеріалами з дерева в тому, що вона не кришиться під час випилювання, легко обробляється, покривається лаком і полірується.
Для випилювання необхідно вибирати якісну фанеру: чисту і однорідну за кольором, без сучків, тріщин і сколів, добре висушену і не покороблену, яка не має на собі частин, уражених гниллю чи грибком.
Деревоволокнисті плити (ДВП) – це матеріал, котрий отримують шляхом гарячого пресування маси, що складається з целюлозних волокон, води, синтетичних полімерів і спеціальних добавок. Волокна отримують шляхом пропарювання та помелу деревної сировини. Під дією великого тиску і високої температури деревні волокна спресовуються в однорідний матеріал.
Сировиною слугують відходи деревообробної промисловості. Для покращення механічних властивостей у масу додають речовини, що зміцнюють її: синтетичні смоли, парафін, церезин, антисептики та інші.
За видом поверхні ДВП буває необроблена або з декором. Декор у свою чергу може наноситись як плівка – ламіноване ДВП, або це може бути фарба – фарбоване ДВП. Товщина найбільш популярного ДВП – 3,5 мм. Узагалі, виробляється ДВП товщиною від 3 до 5 мм.
ДВП застосовують разом із фанерою для виготовлення столярних виробів і меблів. У меблевій промисловості з них найчастіше виготовляють не несучі конструкції, а декоративні та огороджувальні елементи: задні стінки шаф та тумб, дно шухляд тощо.
Тема 2.2. Властивості фанери та ДВП
Будівельна фанера донині є самим застосовуваним матеріалом, широко використовується при будівництві легких споруд. Низька ціна фанери в сукупності з її відмінними техніко-експлуатаційними властивостями робить цей матеріал надзвичайно популярним на будівельному ринку.
Фанера - це шарувата клеєна конструкція, що складається з трьох і більше листів деревини з взаємно перпендикулярним розташуванням волокон в суміжних шарах. Це надає фанері підвищену міцність в різних напрямах, стабільність форми, що є безперечною перевагою в порівнянні з натуральною деревиною. Фанера також, як і деревина, - матеріал, що легко піддається обробці. Поверхня її обробляється різними способами: ламінується, покривається струганим шпоном, фарбами, лаками. Фанера має невелику вагу, легко комбінується з іншими матеріалами, проста в обробці, стійка до перепадів температури, має естетичний зовнішній вигляд. Її міцнісні, теплопровідні і екологічні характеристики набагато вище показників інших деревинно-плиткових матеріалів, таких як ДСП, ДВП.
Деревоволокнисті плити ДВП – це прекрасний листовий обшивочний матеріал для облицювання каркасних перегородок, стін, стель житлових будинків .
Корисним цей матеріал може стати і для домашнього майстра. Незамінні ДВП при влаштуванні підлог в якості прокладного шару під всі види покриття, у тому числі дощатого і щитового паркету, синтетичних покриттів і ленолеум.
ДВП, завдяки підвищеній міцності і водостійкості, незамінні при виробництві меблів, вбудованих шаф, столярних та інших виробів і конструкцій; використовується в автомобільній промисловості; вагонобудуванні, в будівництві, при виробництві тари.
Деревоволокнисті плити (оргаліт), вироблені на підприємстві мокрим способом, є екологічно чистими, тому що у їх виготовленні не включаються синтетичні добавки.
Розпилювання та обробка фанери і ДВП не становлять великих труднощів і можливі за допомогою всіх інструментів, які застосовуються для обробки дерева і дерев'яних поверхонь.
Тема 2.3. Процес розмітки заготовок
Перш ніж почати виготовляти вироби із вищеописаних матеріалів, необхідно позначити контури майбутньої деталі на матеріалі. Жодну, навіть просту, деталь не можна виготовляти на око.
Технологічний процес, у результаті якого на поверхні заготовки намічають контури майбутньої деталі, називають розміткою. Розпочинають розмічання з аналізу форми країв заготовки. Визначають найрівніше ребро, від якого найкраще виконувати розмічання. Це ребро називають базовим, а проведену поблизу базового ребра лінію, від якої виконують розмічання заготовки, називають базовою.
Лінії розмітки – риски – наносять на деревину олівцем. Фіксовані крапки і лінії наносять за допомогою лінійки, кутника, транспортира.
Краще всього для розмітки підходить плоска дерев’яна лінійка з поділками шкали 1 мм. Для визначення відстані від бази до потрібної відмітки на поверхні заготовки лінійку беруть у ліву руку і розміщують її так, щоб поділка, яка відповідає потрібному розміру, співпала б із відповідною базою. Потім гострим олівцем уздовж короткої грані лінійки проводять лінію; необхідна крапка визначається перетином двох (найчастіше перпендикулярних) рисок. Щоб нанести пряму лінію, необхідно зафіксувати дві крапки, а потім з’єднати їх за допомогою лінійки. Якщо розміри деталей перевищують довжину лінійки, то необхідно користуватись рулеткою або складним метром.
Столярний кутник складається із дерев’яної лінійки (пера) та колодки із твердої породи деревини. Із його допомогою проводять перпендикулярні та паралельні лінії. Для цього колодку інструмента щільно притискають лівою рукою до базової кромки і проводять риску по перу кутника. Використання цього інструмента дозволяє гарантувати точність розмітки тільки в тому випадку, коли опора для колодки достатньо довга і вирівняна.
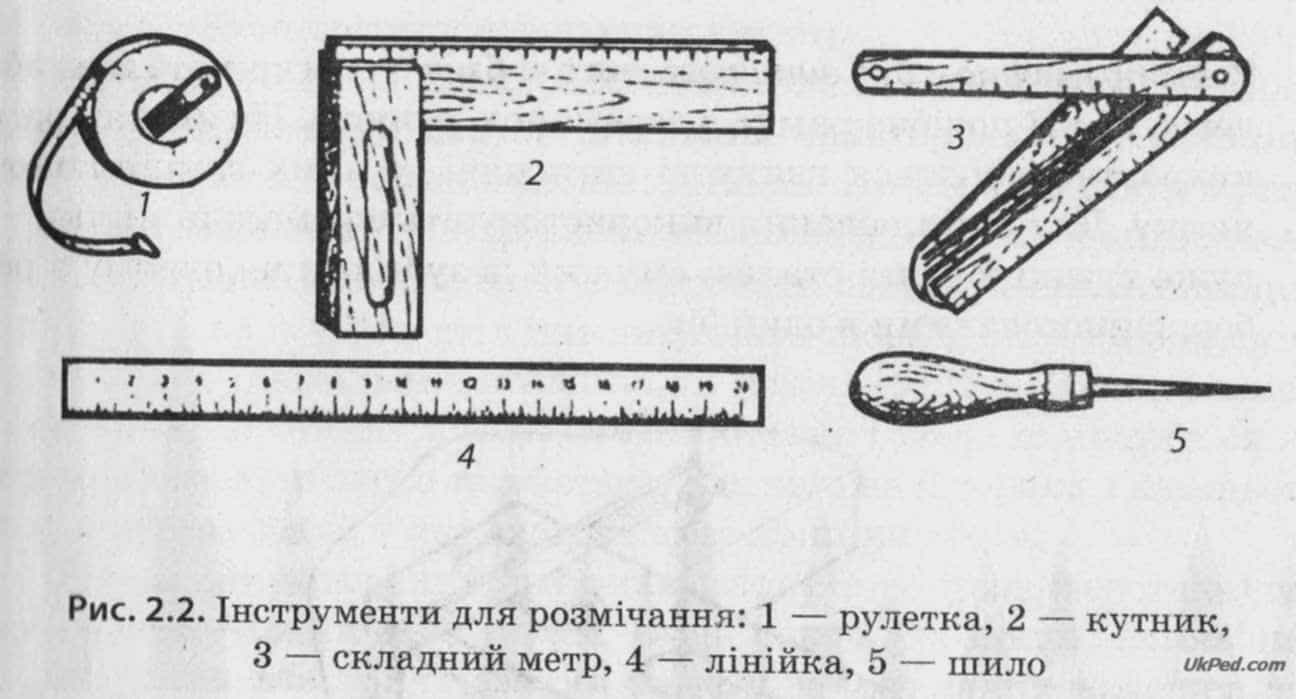
Під час розмічання потрібно передбачити надлишок матеріалу на кінцеву обробку деталей – припуск.
Розмічання великої кількості однакових деталей або деталей, що мають криволінійний контур, роблять за допомогою спеціальних шаблонів, які мають вигляд пластин із такими ж обрисами, як і контур виробу. Використання шаблонів економить час на розмітці, спрощує її, розмітка стає більш точною. Шаблони для розмітки бувають різні за розмірами, формою і конструкцією. Виготовляють шаблони із листової сталі, фанери, твердих деревоволокнистих плит.
Шаблон накладають на фанеру, дошку, брусок, заготовку, а потім олівцем або шилом обводять контури.
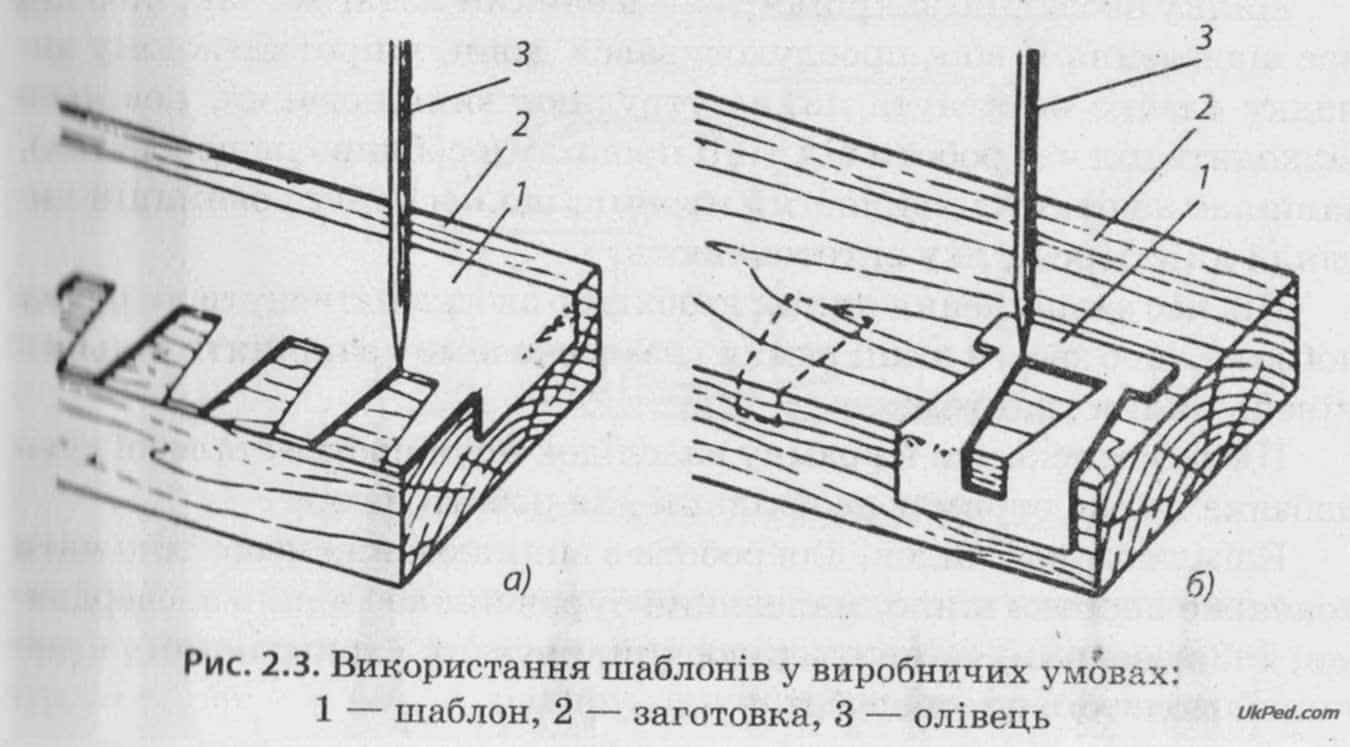
Тема 2.4. Процес пиляння фанери та ДВП
Інструментом для випилювання слугує лобзик – легка металева або дерев’яна П - образна рамка з дерев’яною ручкою. На кінцях рамки розташовуються гвинтові затискачі, у яких закріплюється пилка. Для випилювання використовують спеціальні пилки – дуже вузькі й тонкі сталеві смужки із зубцями на одному з ребер, спрямованими в один бік.
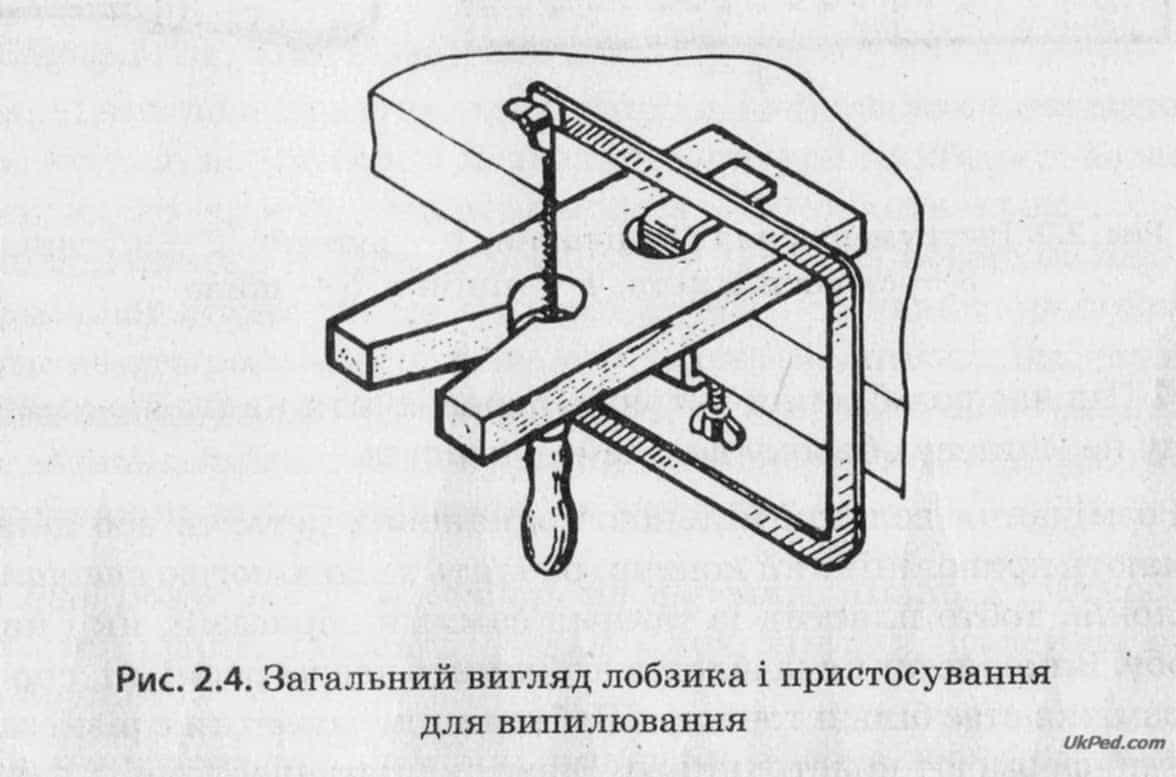
Зубці пилки завжди повинні бути повернуті до зовнішнього боку рамки і спрямовані своїми кутами вниз до ручки.
Пилку необхідно закріпляти з невеликим натягом, так, щоб при відведенні її вбік прослуховувався дзвін, у протилежному випадку слабко натягнута пилка утруднює випилювання, повільно відходить під час роботи від лінії пропилу (особливо на поворотах), залишає нечіткий і хвилястий пропил, щопогіршує зовнішній вигляд і якість речі, що виготовляється.
Під час закріплення пилки необхідно злегка натиснути на ручку лобзика, щоб звести кінці рамки з затискачами і закріпити вільний кінець пилки гвинтом.
Після натискання на рамку внаслідок пружності металевої дуги лобзика пилка отримає необхідний для роботи натяг.
Крім лобзика і пилок для роботи з випилювання необхідно мати тоненьке коротке шило, маленький буравчик або дриль із свердлами, 2-3 невеликих напилка (плоский, круглий і тригранний), невеликий молоток, плоскогубці.
Випилювання лобзиком виконують на спеціальному випилювальному столику (типу «ластівчин хвіст»).
Кріплять його на краю робочого стола за допомогою спеціальних затискачів (струбцин). У шкільних майстернях випилювальні столики кріплять на спеціальних стійках. Це дає можливість встановити столик на потрібній висоті залежно від зросту працюючого.
Якщо необхідно одночасно забезпечити роботу декількох працівників, щоб не псувати стіл і не витрачати кожного разу час на кріплення і зняття випилювальних столиків, їх можна (раз і назавжди) закріпити на одній міцній дошці. Остання легко і швидко кріпиться на робочому столі та легко знімається, для чого на її торцях з нижнього боку зроблені пази, у які входять краї кришки стола.
Під час випилювання працюючий сідає біля стола (верстака) перед випилювальним столиком. Випилюють лобзиком, поклавши підготовлену для випилювання фанеру на підкладну дощечку, що має вигляд ластівчиного хвоста і виступає над краєм стола. У проріз підкладної дощечки вставляють пилочку лобзика і починають пиляти, рухаючи лобзик угору і вниз, перпендикулярно до фанери, притримуючи її лівою рукою. Не можна допускати вібрування фанери, тому що воно може викликати відколи шару деревини і поломку, особливо ажурних і тонких речей.
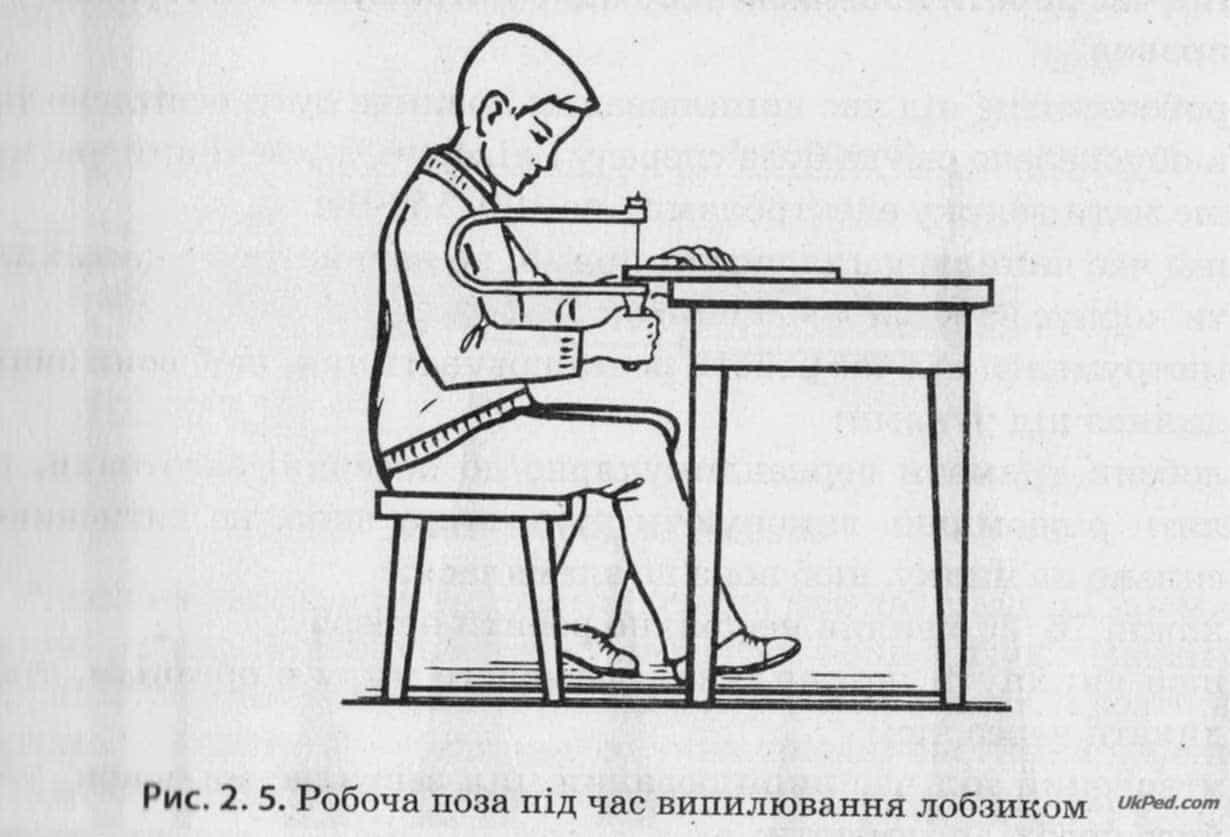
Пилочка пиляє тільки під час руху вниз; при цьому на неї слід злегка натискати. Якщо за малюнком потрібний поворот, то повертають не лобзик, а фанеру, причому круті повороти роблять повільно, не поспішаючи і не натискаючи на лобзик. Щоб випиляти проріз, спочатку шилом проколюють отвір, у який просувають вивільнену від затискача пилочку. Потім її знову затискають і починають роботу. Випилявши отвір, пилочку таким же способом виймають. Для візерунка з багатьма отворами спочатку випилюють отвори, а потім зовнішній контур малюнка.
Від тривалої роботи пилочка нагрівається, тому час від часу її слід охолоджувати, протираючи вологою ганчіркою або роблячи перерву у роботі. З метою попередження швидкого перегрівання також рекомендується робити рухи пилкою на всю її довжину.
Іноді під час роботи буває затискання пилки в деталі. У цьому випадку необхідно трохи повернути пилку вбік і усунути затримку або ж звільнити верхній кінець пилки та висунути її з пропилу. Найчастіше це трапляється, коли пилка має деформовану ділянку у вигляді опуклості, яка заважає і ускладнює подальше випилювання. Для того, щоб виправити пилку, її необхідно покласти на рівну металеву поверхню і легким ударом молотка виправити.
Перестановку пилок у лобзику необхідно робити обережно, щоб попередити їх обламування, особливо у нижнього затискного гвинта.
Під час роботи лобзиком необхідно дотримуватись наступних правил:
- робоче місце під час випилювання повинне бути освітлене таким чином, щоб джерело світла знаходилось спереду і зліва, а у вечірній час краще мати велику електролампу на 100-150 Вт;
- під час випилювання сидіти прямо, не нагинатися і не нахиляти корпус вбік (вправо і вліво);
- інструменти при роботі розташовувати таким чином, щоб вони знаходилися під руками;
- лобзик тримати перпендикулярно до поверхні заготовки, пиляти рівномірно, виконуючи рухи вгору - вниз, не натискаючи сильно на пилку, щоб вона не зламалась;
- кожні 15-20 хвилин необхідно робити перерву;
- щоб уникнути потрапляння деревного пилу в організм, треба дихати через ніс;
- утворений при випилюванні пил застилає малюнок, тому його необхідно змітати;
- для захисту одягу від пилу працювати у фартуху;
- малюнок на матеріал треба переводити чітко, щоб його можна було розглядати, не напружуючи зору;
- спочатку працювати тривалий час лобзиком не рекомендується, оскільки будуть втомлюватися руки, і особливо ліва рука;
- після роботи провітрити кімнату і вологою ганчіркою протерти запилені речі.
15.04.2020р. Тема: Технологія механічної обробки деревини
(2 академічні години)
Добрий день, дорогі учні! Теоретичний матеріал із цієї теми дуже розгалужений та вимагає багато часу на його засвоєння. Однак у шкільних майстернях зазвичай є електрифіковані ручні інструменти, тому краще звернути увагу на особливості їх використання. Як ви думаєте:
- Які деревообробні інструменти належать до електрифікованих? Чому вони називаються електрифікованими?
- Яка енергія використовується в цих інструментах для виконання роботи?
- Яким інструментом - механічним чи електрифікованим - можна швидше та якісніше виконати роботу?
Використання механізмів (наприклад, механічний дриль) поліпшує характеристики інструментів та дає змогу виконувати роботу швидше, ніж за допомогою ручного простого інструменту (коловорот); використання електричного двигуна сприяє швидкому та якісному виконанню технологічних операцій без затрати значних фізичних зусиль. Саме електрифікований інструмент дає можливість у домашніх умовах або в шкільній майстерні виконати роботу за коротший проміжок часу.
У процесі вивчення цієї теми ви повинні засвоїти назви і призначення найпоширеніших видів електрифікованих знарядь праці, а також запам’ятати переваги цих інструментів перед ручними, призначення основних частин, навчитися визначати основні параметри і правила безпечної праці під час користування ними.
Найпродуктивнішим технологічним обладнанням є верстати. І саме вони використовуються на заводах, у столярних цехах та на інших видах підприємств. Деревообробні верстати є продуктивним засобом виробництва. Однак деякі дрібні роботи виконують за допомогою ручного електроінструменту.
Чи завжди потрібно та доцільно використовувати деревообробні верстати під час виготовлення виробів з деревини?
Використання деревообробних верстатів виправдане лише тоді, коли необхідно виконати великий обсяг робіт, виготовити значну кількість виробів. Верстати мають потужні електродвигуни та споживають електроенергії більше, ніж ручні електрифіковані інструменти. Тому для виготовлення дрібних деталей проектованого виробу використовують електролобзик, електрофрезерну машину, електрорубанок та інші інструменти. Для виготовлення виробу можна використовувати також звичайні ручні інструменти в поєднанні з електрифікованими, такий спосіб організації виробництва дешевший. Таким чином, використання верстатів та електрифікованих інструментів повинне бути економічно обґрунтованим.
історії розвитку верстату(мал. 75).

Мал. 75. Орієнтовні слайди для презентації
Також по змозі слід продемонструвати роботу сучасних верстатів за допомогою відеороликів з відеосервісів:
- Комбінований деревообробний верстат Д250;
- Майстер Практик 2500;
- фрезерний верстат Корвет-86;
- рейсмусовий верстат Format-4 Exact 63;
- фрезерний верстат з ЧПУ 4-осьовий;
- CNC-1500 - токарний верстат із ЧПУ для різьблення по дереву;
- оброблювальний центр Biesse Rover 24; Biesse Skipper 130.
Людина, прагнучи полегшити технологію виготовлення виробів, поліпшити їх якість та здешевити вартість, сконструювала різні електрифіковані знаряддя праці. Сьогодні широкого використання в побуті та на промислових підприємствах набули електричні пилки, лобзики, дрилі, шліфувальні та полірувальні машини тощо.
Електрифікованим інструментом (малою механізацією) називають такий ручний інструмент, у якому різці приводяться в рух від електродвигуна, а весь інструмент робітник переміщує вручну. Завдяки компактності і невеликій масі (5.15 кг) електроінструментів їх застосовують там, де не можна використати деревообробні верстати (у ремонтних і монтажних роботах, а також частково в складальних).
Так, для шліфування деревини використовують шліфувальні машинки, дисковими пилками розпилюють заготовки з деревини та ДСП, електричним лобзиком випилюють складні криволінійні поверхні. Електрична свердлильна машина «допоможе» виготовити отвори в деталях. Всі ці електроінструменти складаються з трьох основних частин: електродвигуна, корпусу і різального інструмента. Розповідати про основні частини найдоцільніше після демонстрування самих знарядь.
Для прикладу можна розглянути найпоширеніший у навчальних майстернях та побуті електричний дриль (мал. 76). В нерухомому статорі електродвигуна, який часто є корпусом електроінструменту, обертається циліндричний ротор, до якого інколи кріплять різальний інструмент. Вал ротора закріплюється в корпусі на підшипниках. Корпус скріплює всі частини механізмів, захищаючи їх від зовнішніх пошкоджень і забруднення. На корпусі розміщено ручки, пусково-зупинні кнопки, опорні панелі, напрямну лінійку, захисні та інші пристрої.

Мал. 76. Основні вузли електричного дриля: 1 - патрон для кріплення свердла або іншого різального інструмента; 2 - редуктор для зменшення частоти обертання патрона; 3 - електродвигун; 4 - кнопка «Пуск»; 5 - кнопка перемикання режимів роботи; 6 - корпус; 7, 8 - електричні компоненти для оптимізаціі роботи; 9 – шнур
Електрифіковане знаряддя праці має певні механічні і електричні параметри, які записані в паспорті до інструмента та на таблиці, що кріпиться на його корпусі.
Основні параметри
|
Інструмент та його марка
|
Електропилка
| |
Діаметр диска, мм
|
180
|
Найбільша глибина пропилу, мм
|
60
|
Кількість обертів за хвилину
|
2820
|
Швидкість різання, м/хв
|
26,6
|
Вага, кг
|
11,0
|
Напруга, В
|
220
|
Потужність, кВт
|
0,5
|
Мал. 77. Таблиця параметрів
Слід особливо наголосити на необхідності суворо дотримуватися правил безпечної праці під час роботи з електрифікованими знаряддями праці для обробки деревини. Треба звернути увагу учнів на те, що струмопровідні частини інструмента мають бути завжди надійно ізольовані, а інструмент, який працює, заземлений. Зважаючи на велику кількість обертів різальних частин електрифікованих знарядь праці, користуватися ними потрібно дуже обережно.
Сьогодні технічний прогрес сприяє модернізації верстатів і обробка на верстатах дедалі більше замінює ті види робіт, які раніше виконувалися лише вручну. Основна мета модернізації полягає в подальшому покращенні умов праці робітника і підвищенні її економічних показників. Модернізовані верстати називають комп’ютеризованими. Саме поєднання комп’ютера та верстата дозволило швидко виконувати складні оздоблювальні роботи, одиничні замовлення виробів з деталями складної форми тощо.
Висока технологічна точність верстатного обладнання досягається раціональним поєднанням принципової схеми, конструкції вузлів, вибором матеріалів і технології виробництва. Так, з’явилися деревообробні багатоопераційні верстати із числовим програмованим управлінням (ЧПУ).
Завдяки програмованому керуванню, такі верстати дуже мобільні і дозволяють швидко змінювати положення робочого органу та інструмента. Для прикладу учням можна продемонструвати ряд обладнання, використавши фотографії або малюнки таких верстатів. Це можуть бути зображення сучасних токарних верстатів, фрезерних верстатів для різьблення по дереву (мал. 78) тощо.
Розглядаючи токарний верстат із ЧПУ, важливо знати, як різальний інструмент використовують кінцеві фрези або комбінують кінцеві і дискові фрези (мал. 79). Під час обробки деталі кінцевою фрезою можна отримати різний фігурний профіль на заготовці. Шлях переміщення фрези і швидкість обертання заготовки задається за допомогою програмного забезпечення залежно від форми майбутньої деталі.

Мал. 78. Фрезерно-гравірувальний верстат із ЧПУ для різьблення по дереву

Мал. 79
Надалі доцільно розглянути окремі питання безвідходного виробництва в галузі деревообробки. Слід наголосити, що, природно, деревина була завжди дуже популярна в будівництві, але в сучасному житті цей попит побив усі рекорди. Це призвело до того, що, разом з активним пізнанням лісоматеріалів, почався етап посиленого їх збереження як у питанні обсягів вирубки площ, так і в плані деревообробки.
Під час виготовлення виробів з деревини дістають багато відходів. Виникає питання: Куди ж діваються відходи (деревний пил, стружка, гілки, пеньки і кора)? Відповідь досить проста. Стружку і тріску використовують на етапі виготовлення деревостружкових плит (ДСП, ДВП, ОСП та ін.) Деревний пил проходить етап переробки в деревне борошно. Надалі це борошно застосовують для виготовлення фільтрів, а кору переробляють у добриво (мульчу), а також використовують у целюлозній промисловості.
Також сьогодні популярним є використання відходів деревообробки у виготовленні виробів з малих шматків (обрізків), пресування пелетів (пресованих гранул з тирси для опалювання) (мал. 80).

Мал. 80. Пелети
Звідси висновок: деревина використовується майже на 90 %. Це свідчить про те, що нові деревообробні технології допомагають людям правильно витрачати лісоматеріал і застосовувати його якомога оптимальніше.
Домашнє завдання. Опрацювати теоретичной матеріал, зробити коротенький конспект у зошитах.
Фото відповідей надсилайте у вайбер 099-63-72-507
або на ел. пошту marinalutay84@gmail.com
Гарного вам настрою та будьте здорові!
8.04.2020р. Тема: Технологія шліфування виробів
(2 академічні години)
Дорогі учні! Опрацюйте, будь ласка, теоретичний матеріал, дайте відповідь на тестові завдання в вашому робочому зошиті. Тестові завдання знайдете внизу. Відповіді знайдете в тексті.
Фото відповідей надсилайте у вайбер 099-63-72-507
або на ел. пошту marinalutay84@gmail.com
Гарного вам настрою та не хворійте😉!
Щоб надати виробам привабливого зовнішнього вигляду, підготувати їх до оздоблення і при цьому досягти більш якісного оброблення, ніж напилками, поверхню виробів шліфують. Виконують таку технологічну операцію шліфувальною шкуркою. Це багаторізцевий різальний інструмент, який складається з наклеєних на поверхню цупкого паперу або тканини дуже твердих дрібненьких частинок у вигляді зерен з гострими вершинами (мал. 82).
Матеріали, з яких виготовляються такі зерна, називають абразивами.
Під час руху шліфувальної шкурки по оброблюваній поверхні кожне зерно діє як клин різального інструмента, зрізуючи при цьому її нерівності.
Від розмірів та кількості твердих частинок, наклеєних на одному квадратному сантиметрі шліфувальної шкурки, залежить якість обробки. Що більша кількість зерен припадає на один квадратний сантиметр поверхні шліфувальної шкурки, то з більшою чистотою здійснюється обробка заготовки або виробу.
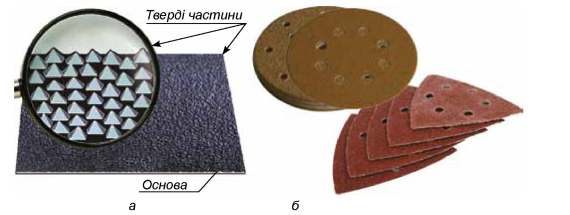
Мал. 82. Шліфувальна шкурка: а - схематичне зображення; б - загальний вигляд
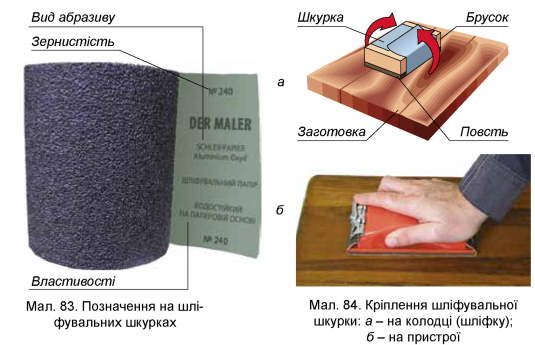
Для вищої якості обробки поверхні необхідно використовувати нову шліфувальну шкурку. На звороті аркуша або стрічки цього інструмента містяться певні написи: відомості про виробника, зернистість шкурки, умови її використання тощо (мал. 83).
При виборі шліфувальної шкурки слід звернути увагу на зернистість, яка позначається числом або числом з літерою. Що більше число, то більша кількість зерен наклеєна на одному квадратному сантиметрі основи шліфувального паперу, то дрібніші зерна, а значить, з більшою чистотою можна оброблювати поверхню виробу. Для шліфування виробів з деревних матеріалів краще застосовувати шліфувальні шкурки з номерами 100.. .140.
Шліфують поверхню деревини чи фанери за допомогою шліфувальної колодки (шліфка) або спеціального пристрою, на яких кріпиться шліфувальна шкурка (мал. 84).
Напрямок шліфування повинен збігатися з напрямком волокон деревини (мал. 85, а). Якщо шліфувати поперек волокон (мал. 85, б), утворяться подряпини. Спочатку вони будуть майже непомітними, але після
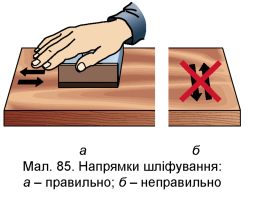
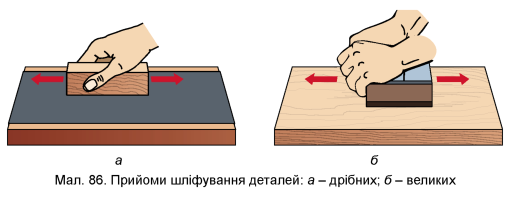
покривання виробу лаком чітко вирізнятимуться й зіпсують зовнішній вигляд виробу.
Щоб зачистити дрібні деталі, їх рухають по шліфувальній шкурці. Великі деталі шліфують переміщенням бруска з шліфувальною шкуркою вздовж волокон деревини заготовки (мал. 86).
Нині великого поширення як на виробництві, так і в побуті набуло використання електрифікованих шліфувальних машин (мал. 87). Про будову, призначення та прийоми роботи такими інструментами ти дізнаєшся в подальшому на уроках трудового навчання.
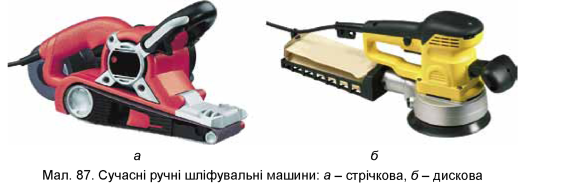
Під час шліфування виробів необхідно додержуватися таких правил безпечної праці:
1. На робочому місці не повинно бути нічого зайвого.
2. Шліфування площинних заготовок виконувати на підкладній дошці.
3. Не торкатися руками шліфувальної шкурки та гострих частин заготовки.
4. Не здмухувати відходів, змітати їх тільки спеціальною щіткою.
ПРАКТИЧНА РОБОТА № 3 Шліфування виробів
Обладнання і матеріали: вироби, виготовлені на попередніх уроках, шліфувальна шкурка № 100.140, шліфок.
Послідовність виконання роботи
1. Підготуй раніше виготовлені вироби.
2. Визнач нерівності на плоских поверхнях деталей.
3. Відшліфуй ці поверхні.
4. Склади деталі в конструкцію (якщо виріб складається з кількох деталей).
5. Перевір якість виконаної роботи. Оздоблювальні роботи виконай після вивчення наступних тем.

шліфування, шліфувальна шкурка, абразив, зерно, шліфок.

Абразивний матеріал - дуже твердий зернистий матеріал, який застосовують для шліфування, полірування, заточування.
Шліфок - пристрій, призначений для кріплення шліфувальної шкурки.

1. Що спільного та в чому відмінність у технології обробки деревинних матеріалів напилком та шліфувальною шкуркою?
2. Як залежить якість обробки поверхні виробу від розмірів зерен шліфувальної шкурки?
3. Як правильно шліфувати поверхню деревинних матеріалів?
4. Яких правил безпечної праці потрібно дотримуватися під час шліфування виробів?
Тестові завдання
1. Який різальний інструмент використовують для чистової обробки деревних матеріалів?
А ніж Б пилку
В шліфувальну шкурку Г рубанок
2. Для шліфування виробів з деревних матеріалів краще з стосовувати шліфувальні шкурки з номерами
А 60.80 В 160.200
Б 100.140 Г 220.240
3. Пристосування, призначене для кріплення шліфувальн шкурки, називається
А шерхебель В рашпіль
Б шліфок Г абразив
4. Як позначається зернистість шліфувальної шкурки?
А словом В числом
Б літерою Г числом і літерою
5. У якому напрямку слід шліфувати заготовку?
А уздовж волокон
Б поперек волокон В під кутом до волокон Г коловими рухами
01.04.2020р. Тема: Технологія нарізання внутрішньої
і зовнішньої різьби (2 академічні години)
Дорогі учні! Опрацюйте, будь ласка, теоретичний матеріал, дайте відповідь на тестові завдання в вашому робочому зошиті. Тестові завдання знайдете внизу. Відповіді знайдете в тексті.
Фото відповідей надсилайте у вайбер 099-63-72-507
або на ел. пошту marinalutay84@gmail.com
Гарного вам настрою!
У сучасному виробництві широко використовують високопродуктивні методи нарізання різьби на металорізальних верстатах за допомогою різьбонарізних інструментів (мал. 110). Успішно отримують різьбу і за допомогою інструментів для накатування та ін. Однак, виконуючи слюсарні роботи, переважно доводиться нарізати різьбу ручним способом.
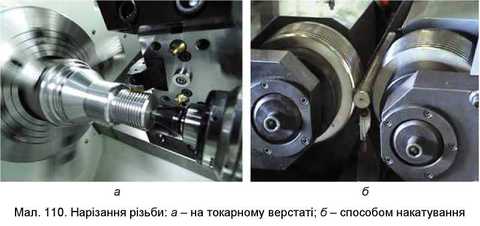
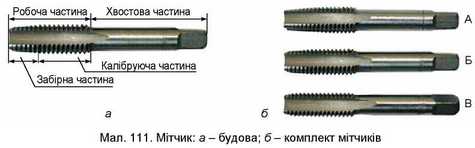
Для нарізання різьби в отворах застосовують мітчики, а для нарізання зовнішньої різьби - плашки різної конструкції.
Мітчик (мал. 111) - різальний інструмент у вигляді загартованого гвинта із кількома прорізаними на ньому поздовжніми прямими або гвинтовими канавками, які утворюють різальні кромки. Мітчик працює при двох одночасних рухах: обертовому (мітчика або заготовки) та поступальному (уздовж осі мітчика). Мітчик має робочу частину і хвостову частину (хвостовик).
Робоча частина мітчика складається із забірної і калібрувальної частин. Забірна частина - це передня конусна частина, яка першою входить в отвір і здійснює основну роботу різання. Калібрувальна частина спрямовує мітчик в отвір і остаточно завершує нарізання різьби (калібрує різьбу).
Хвостова частина - це стрижень для закріплення мітчика в патроні або воротку; квадрат служить для передачі крутного моменту.
Ручні (слюсарні) мітчики служать для нарізання різьби ручним способом. Їх виготовляють комплектами. У комплект, що складається з трьох мітчиків, уходять чорновий, середній та чистовий. Чорновий мітчик має на хвостовій частині одну кругову риску (канавку), середній - дві й чистовий - три риски (мал. 111, б). На мітчиках указується також тип різьби та її розмір. За зовнішнім виглядом мітчики одного комплекту відрізняються тим, що чорновий має більшу забірну частину (конус) і зрізану різьбу на калібрувальній частині, а чистовий - незначний забірний конус і повний профіль різьби на калібрувальній частині.
В основному використовують чорнові та середні мітчики. Чистові мітчики використовують під час нарізання різьби великого діаметра з великим кроком.
Велике значення при нарізанні різьби має правильний вибір діаметра. Якщо він більший, ніж потрібно, то внутрішня різьба не матиме повного профілю, а при меншому - вхід мітчика в отвір утруднений, що спричинює зривання ниток різьби або заклинювання й поломку мітчика.
Вибираючи діаметр свердла для отвору під різьбу, слід користуватися даними таблиць.
Після свердління отвору під різьбу деталь закріплюють у лещатах, чорновий мітчик змащують мастилом і у вертикальному положенні, контролюючи кутником, уставляють в отвір (мал. 112, а). Надівши на мітчик вороток і злегка притиснувши його до деталі, обережно повертають вороток, поки мітчик не вріжеться в метал і його положення не стане стійким (мал. 112, б). Після одного-двох повних обертів зворотним рухом мітчика на чверть його оберту ламають стружку. Закінчивши нарізання, обертанням воротка у зворотному напрямку викручують мітчик.
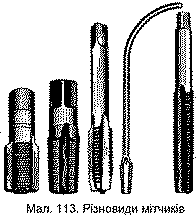
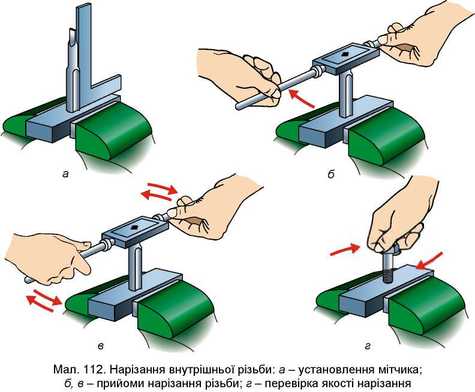
Другий і третій мітчики змащують мастилом і почергово вводять в отвір без воротка. Після того як мітчик установиться по різьбі, накладають вороток і продовжують нарізання різьби. Якість різьби в отворі можна перевірити, закрутивши в отвір болт відповідного діаметра (мал. 112, г).
Для нарізання різьби використовують різні за конструкцією мітчики (мал. 113).
Конструкція плашки - інструмента, який застосовується для нарізання зовнішньої різьби, аналогічна конструкції мітчика. Плашка - це загартована гайка зі стружковими канавками, які утворюють різальні грані (мал. 114, а).
Робоча частина плашки складається із забірної та калібрувальної частин. Її призначення таке саме, як і мітчика.
Для нарізання різьби використовують плашки різних конструкцій.
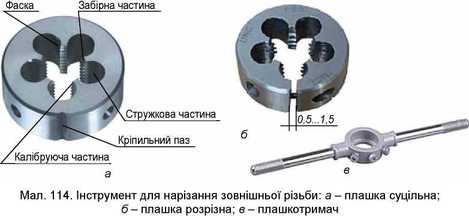
У шкільних майстернях ти будеш користуватися суцільними (мал. 114, а) та розрізними (мал. 114, б) плашками.
Суцільні плашки застосовують під час нарізання різьби за один прохід діаметром до 52 мм. Вони мають велику жорсткість і забезпечують карбування чистої різьби, але порівняно швидко спрацьовуються.
Розрізні (пружні) плашки мають проріз від 0,5 до 1,5 мм.
Перед нарізанням різьби кінець стержня на всю довжину нарізання обточують до потрібного діаметра, а на самому кінці знімають фаску. Стержень під різьбу повинен мати чисту поверхню. Не можна нарізати різьбу на стержнях, покритих окалиною чи іржею, бо в цьому випадку дуже спрацьовуються плашки та погіршується якість різьби.
Під час нарізання різьби плашками, як і під час нарізання мітчиками, у результаті деформації під дією сили різання діаметр заготовки збільшується. При цьому збільшується тиск на калібрувальну частину, що може призвести до зриву різьби або поломки плашки.
Щоб запобігти цим явищам і отримати доброякісну різьбу при виготовленні стержня, його діаметр роблять на 0,2...0,4 мм меншим від зовнішнього діаметра різьби. Якщо ж діаметр стержня буде значно меншим від діаметра зовнішньої різьби, то різьба буде неповною. Значення рекомендованих діаметрів отворів і стержнів під час нарізання внутрішньої та зовнішньої різьби подано в таблиці 2.
Таблиця 2. Діаметри отворів і стержнів для нарізання метричної різьби (мм)
№
пор.
|
Позначення
різьби
|
Крок
різьби
|
Діаметр отвору
|
Діаметр стержня
| ||
сталь,
латунь,
алюміній
|
бронза,
чавун
|
наймен
ший
|
найбіль
ший
| |||
і
|
М3
|
0,50
|
2,5
|
2,5
|
2,95
|
2,98
|
2
|
М4
|
0,70
|
3,3
|
3,2
|
3,90
|
3,95
|
3
|
М5
|
0,80
|
4,2
|
4,1
|
4,85
|
4,95
|
4
|
М6
|
1,00
|
5,0
|
4,9
|
5,80
|
5,90
|
Продовження таблиці 2
№
пор.
|
Позначення
різьби
|
Крок
різьби
|
Діаметр отвору
|
Діаметр стержня
| ||
сталь,
латунь,
алюміній
|
бронза,
чавун
|
наймен
ший
|
найбіль
ший
| |||
5
|
М8
|
1,25
|
6,7
|
6,6
|
7,80
|
7,90
|
6
|
М10
|
1,50
|
8,4
|
8,3
|
9,75
|
9,85
|
7
|
М12
|
1,75
|
10,1
|
10,0
|
11,76
|
11,88
|
8
|
М14
|
2,00
|
11,8
|
11,7
|
13,70
|
13,82
|
9
|
М16
|
2,00
|
13,8
|
13,7
|
15,70
|
15,82
|
10
|
М18
|
2,50
|
15,3
|
15,1
|
17,70
|
17,82
|
11
|
М20
|
2,50
|
17,3
|
17,1
|
19,72
|
19,86
|
Перед нарізанням різьби стержень закріплюють у лещатах так, щоб його кінець виступав над рівнем губок лещат на 15...20 мм більше від довжини нарізуваної частини (мал. 115, а). Потім на торець стержня накладають під кутом 90° закріплену в плашкотримачі плашку і з невеликим натиском починають нарізати різьбу, повертаючи плашкотримач короткими рухами за годинниковою стрілкою (мал, 115, б, в).
Усі слюсарні операції на підриємствах виконує слюсар. Це робітник, який обробляє метали ручним або механічним інструментом. Слюсар -дуже розповсюджена і багатопланова професія. Робота слюсаря необхідна на всіх етапах створення, експлуатації та ремонту різноманітної техніки.
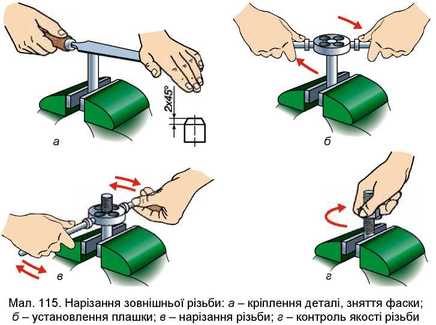
З приходом у наше життя нових будівельних матеріалів і сучасних технологій такі знайомі нам металеві труби відступили на другий план. Зараз більш популярними є труби з металопластику, поліпропілену або поліетилену. Проте в деяких випадках застосування металевих труб просто необхідне. Це зумовлено тим, що вони є універсальними, їх можна використовувати в будь-яких умовах.
Звичайно ж, виникає необхідність з’єднувати труби між собою. Варіантів усього два - зварювання і різьбове з’єднання. Для зварювання потрібен зварювальний апарат. А ось різьбу цілком під силу нарізати самостійно. Для цього використовують ручні (мал. 117, а) та електричні (мал. 117, б) трубні клупи. Клуп дозволяє нарізати різьбу в місцях, де важко це виконати плашкою. Особливо популярний ручний клуп з тріскачкою. Працюючи ним, можна, не знімаючи рукоятки з утримувача, повертати важіль після кожного витка (мал. 117, в).
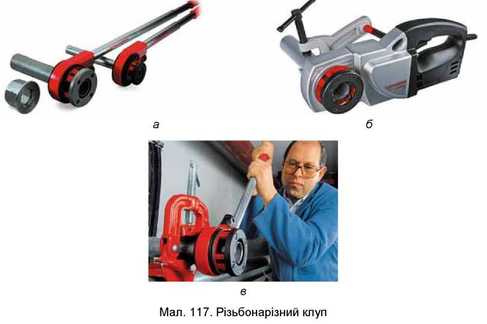
Мітчик, плашка, калібруюча частина, забірна частина.
Вороток - пристрій для кріплення мітчика.
Мітчик - інструмент для нарізання різьби в отворі. Плашка - інструмент для нарізання різьби на стержні. Плашкотримач - пристрій для кріплення плашки.
1. Які інструменти використовують для нарізання зовнішньої та внутрішньої різьби?
2. Яким повинен бути отвір для нарізання різьби?
3. Що спільного у свердла, мітчика, плашки?
4. З якою метою під час нарізання різьби плашку або мітчик потрібно періодично повертати на півоберта назад?
Тестові завдання
1. Для чого під час нарізання різьби через 1-2 оберти воротка роблять півоберта назад?
А щоб полегшити роботу Б щоб сколоти стружку
В щоб забезпечити потрібний крок різьби
2. Для нарізання якої різьби призначений зображений мітчик?

А метричної діаметром 5 мм та кроком 1,75 мм Б метричної діаметром 12 мм та кроком 1,75 мм В метричної діаметром 12 мм та кроком 5 мм
3. Який мітчик застосовують для першого проходу під час нарізання різьби?

А мітчик 1 Б мітчик 2 В мітчик 3
4. На якому малюнку зображено вороток для мітчика?
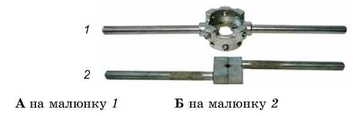
5. На якому малюнку правильно показано початок нарізання різьби мітчиком?
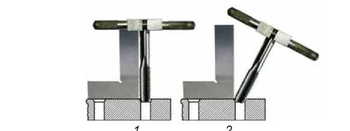
А на малюнку 1
Б на малюнку 2
6. Який кут профілю має метрична різьба?
А 45° Б 50° В 55° Г 60° Д 65°
7. Від чого залежить діаметр стержня та отвору при нарізанні різьби?
А від матеріалу, у якому виконують отвір
Б від діаметра різьби, яку мають нарізати
8. Який технологічний процес називають зенкуванням?
А обробку вхідної частини отвору для знімання фасок, задирок
Б обробку вихідної частини отвору для знімання фасок, задирок, а також утворення заглиблень під головки болтів, гвинтів і заклепок
В обробку вхідної або вихідної частини отвору для утворення заглиблень під головки болтів, гвинтів і заклепок
Г правильної відповіді немає
25.03.2020р. Тема: Технологія свердління (2 академічні години)
Дорогі учні! Опрацюйте, будь ласка, запропонований матеріал, дайте відповідь на тестові завдання в вашому робочому зошиті. Тестові завдання внизу. Відповіді знайдете в тексті.
Фото відповідей надсилайте у вайбер 099-63-72-507
або на ел. пошту marinalutay84@gmail.com
Гарного вам настрою!
Одним з різновидів різання є свердління деревини, металу та інших конструкційних матеріалів. Виконують його за допомогою різних за конструкцією свердел (мал. 71).
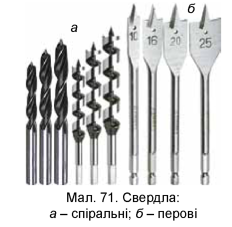
Проте спільним для них є те, що всі вони мають три основні частини: різальну, робочу і кріпильну (мал. 72). На кріпильній частині зазначається діаметр свердла та марка сталі, з якої його виготовлено.

![]() | ![]() |
Мал. 73. Конструкція робочої частини свердла: а - різальні кромки; б - гвинтові канавки; в - спіральні стрічки
|
Мал. 74. Утворення стружки при свердлінні: 1 - свердло; 2 - стружка; 3 - заготовка
|
Різальна частина спірального свердла має дві різальні кромки у формі клина (мал. 73, а).
Заглиблюючись у деревину, різальні кромки зрізують певний її шар. Між ними вздовж робочої поверхні розміщені гвинтові канавки (мал. 73, б), за допомогою яких зрізані частинки деревини відводяться на поверхню заготовки у вигляді стружки (мал. 74).
Робоча частина свердла має дві спіральні стрічки, призначені для спрямування свердла по отвору та зменшення тертя його об стінки.
Його кріпильна частина - хвостовик слугує для закріплення свердла в певному пристрої або механізмі.
Для обертання свердла застосовують механічні та електрифіковані інструменти. Найзручнішими з ручних інструментів є коловорот і дриль (мал. 75).
Обертаючи ручку коловорота чи дриля, свердлу надають обертального руху, а натискуючи на упор - поступального. За рахунок цих двох рухів зрізані частини матеріалу у вигляді стружки виходять на поверхню заготовки.
![]() |
Мал. 75. Ручні свердлильні інструменти: а - коловорот; б - ручний дриль. 1 - упорна ручка; 2 - ручка для обертання; 3 - патрон; 4 - ручка допоміжна
|
![]() | ![]() |
Мал. 76. Свердло, закріплене в патроні
|
Мал. 77. Розмічання центру отвору
|
Свердло підбирають залежно від діаметра отвору, зазначеного на кресленні. Вибравши свердло, його вставляють і щільно затискають у патроні інструмента (мал. 76).
Для свердління заготовку закріплюють у затискачах верстака або інших затискних пристроях. Перш ніж починати свердління, на заготовці розмічають центр майбутнього отвору. За допомогою лінійки і кутника намічають під прямим кутом дві лінії, що перетинаються. Точка перетину є центром майбутнього отвору. Щоб свердло на початку свердління не спорснуло з розміченого центра, центр наколюють шилом (мал. 77).
Центр свердла ставлять у наколотий шилом отвір і обертанням ручки коловорота або дриля приводять у рух патрон зі свердлом. Під час свердління необхідно стежити за тим, щоб свердло було розміщено під прямим кутом до площини заготовки (мал. 78-79).
На початку свердління отворів коловоротом або дрилем свердло обертають повільно. При наскрізному свердлінні свердло виходить з протилежного боку заготовки і може відколювати верхні шари деревини, що псує заготовку. Щоб уникнути цього, під заготовку слід підкладати дерев’яну підкладку, а свердло обертати з меншим натиском на упор. При свердлінні великої кількості глухих отворів на задану глибину використовують обмежувачі. Їх кріплять на потрібній відстані від вершини різальної частини свердла (мал. 80).
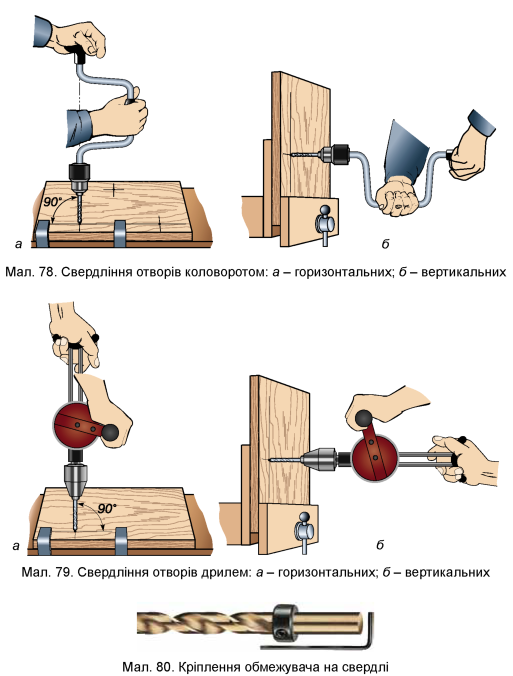
Для полегшення виконання свердлильних робіт і підвищення продуктивності праці промислові підприємства випускають велику кількість різних видів ручних електричних дрилів (мал. 81). Про особливості роботи ними ти дізнаєшся в подальшому на уроках трудового навчання.
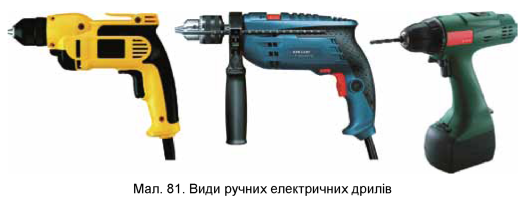
Свердління отворів виконують у такій послідовності:
1. Розмітити на заготовці центри отворів згідно з кресленням.
2. Наколоти шилом центри отворів.
3. Підібрати необхідний діаметр свердла.
4. Закріпити свердло в патроні.
5. Закріпити заготовку на верстаку разом з підкладкою.
6. Просвердлити отвори.
7. Зачистити поверхню шліфувальною шкуркою.
8. Перевірити якість виконання робіт.
Під час свердління необхідно дотримуватися таких правил безпечної праці:
1. Працювати дозволяється тільки справним інструментом.
2. Свердло слід встановлювати правильно, без перекосів, та міцно затискати в патроні.
3. Заготовку слід надійно закріпити на верстаку.
4. Рухи при свердлінні повинні бути плавними.
5. Не можна під час свердління притримувати свердло руками.
6. Не можна перевіряти якість свердління отвору пальцями.
7. Заборонено здмухувати стружки з отвору.
8. Не можна тримати коловорот або дриль свердлом до себе.
свердло, свердління, спіральна канавка, коловорот, дриль, обмежувач.


Гвинт - стержень, що має на своїй поверхні виступи і впадини у вигляді спіралі.
Глухий отвір - отвір, що має обмежену глибину.
Механізм - пристрій, що перетворює або передає рух. Наскрізний отвір - отвір, що проходить через усю заготовку з кінця в кінець з виходом назовні.
Обмежувач - пристрій, за допомогою якого регулюється глибина отвору.
Свердло - різальний інструмент для виконання отворів у деревині, металі та інших матеріалах.
Спіраль - металева смуга чи дріт, закручені по кривій лінії.
1. Які бувають свердла за призначенням?
2. Якими способами одержують отвори в деревині?
3. Як правильно свердлити отвори дрилем, коловоротом?
4. Як виконати наскрізний і глухий отвори?
5. Яка причина сколювання нижнього шару деревини при наскрізному пилянні? Як запобігти цьому явищу?
6. Яких правил безпеки праці слід дотримуватися під час свердління отворів?
Тестові завдання
1. Перед свердлінням центри отворів наколюють шилом, щоб А було краще видно
Б не спорснуло свердло на початку свердління В полегшити свердління
2. Для свердління фанери свердло потрібного діаметра затискають у
А лещатах Б патроні
В столярних затискачах Г плоскогубцях
3. При свердлінні отворів на зазначену глибину використовують
А шило Б обмежувач В патрон
4. При свердлінні наскрізних отворів під заготовку підкладають прокладку для того, щоб
А трохи підняти заготовку над верстаком Б заготовка не рухалась
В не відколювались шари деревини на місці виходу свердла
Г підвищити продуктивність праці
Д не псувати кришки верстака при наскрізному свердлінн
Немає коментарів:
Дописати коментар